非破壊検査とは?種類・メリット・5つのデメリット・AI活用事例を徹底解説!
最終更新日:2025年08月20日
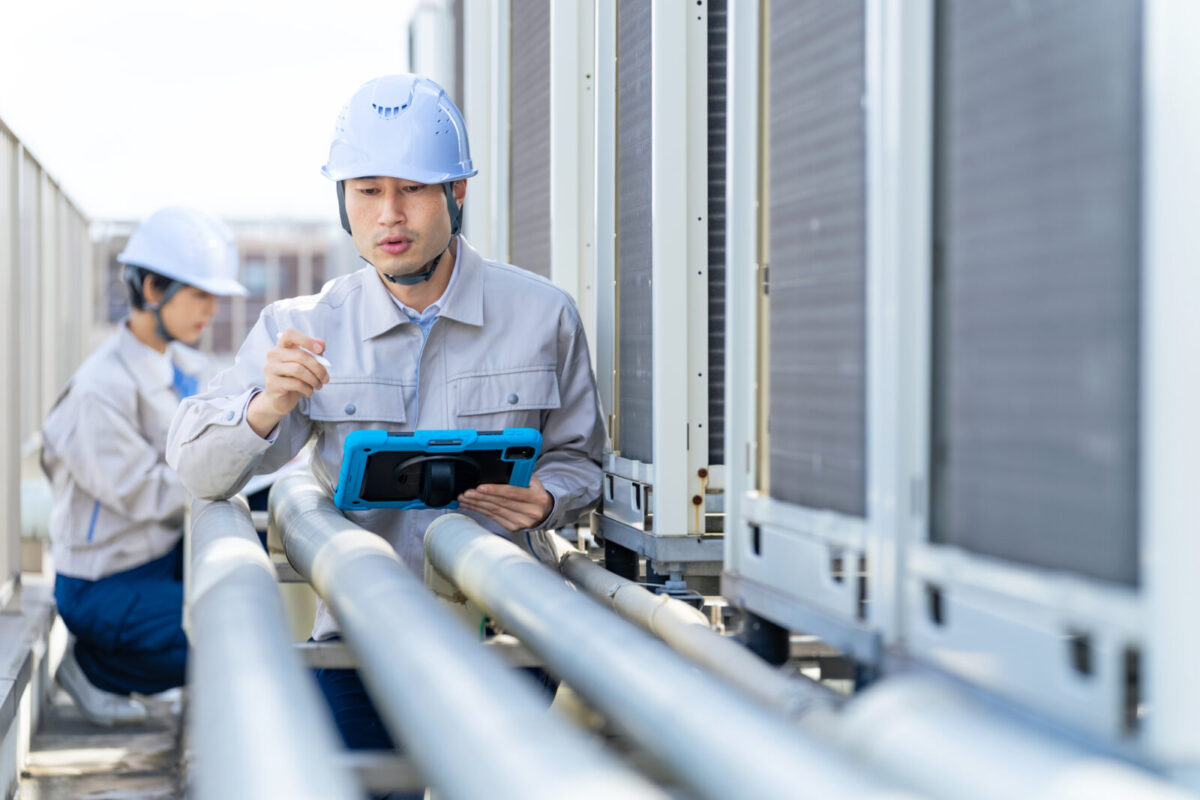
非破壊検査は、製品や構造物の欠陥や劣化を、検査対象を破壊せずに調べるの技術です。非破壊検査は、製造現場やインフラ設備の安全性を確保するうえで欠かせません。
その重要な非破壊検査ですが、近年では、
外観検査に強いAI会社の選定・紹介を行います
今年度AI相談急増中!紹介実績1,000件超え!
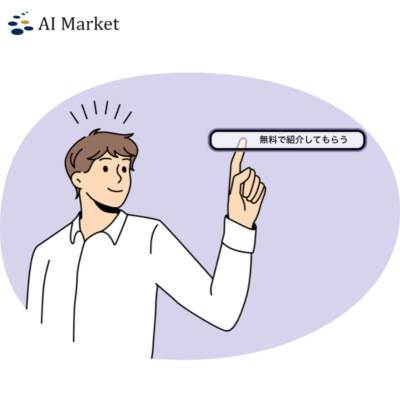
・ご相談からご紹介まで完全無料
・貴社に最適な会社に手間なく出会える
・AIのプロが貴社の代わりに数社選定
・お客様満足度96.8%超
完全無料・最短1日でご紹介 外観検査に強いAI会社選定を依頼する
AI開発会社をご自分で選びたい場合はこちらで特集していますので併せてご覧ください。
目次
非破壊検査とは?
非破壊検査(NDT: Non-Destructive Testing)とは、検査対象の構造物や機器を「破壊することなく」内部の欠陥や劣化の状況を調べる検査技術です。非破壊検査を実施する際には、目視検査を始め、主に超音波や放射線、レーダーが使用され、製品の内部構造や欠陥を高精度で検出します。
非破壊検査の目的は「品質評価」と「寿命評価」で、設備やインフラの長期的な安全性を担保するうえで欠かせません。
- 品質評価:製品の製造時に欠陥がないか確認する
- 寿命評価:長期間使用する設備が安全に使えるか確認する
非破壊検査は幅広い機械や建築物の検査で活用され、原子力発電所からビル・鉄道・橋梁・ガス管や水道管など埋設されたインフラ設備まで、さまざまな検査シーンでの活用が進められています。
関連記事:「AIはガス水道業界をどう変える?活用方法・メリット・事例を徹底解説!」
非破壊検査の主な種類
非破壊検査は、対象物の欠陥の種類や位置によって、適した検査手法が異なります。以下は、代表的な非破壊検査の種類です。
内部欠陥 | 放射線透過試験(RT: Radiographic Testing) | X線やガンマ線を利用して、内部欠陥を検出 |
超音波探傷試験(UT: Ultrasonic Testing) | 超音波を対象物に照射し、その反射波を利用して内部の欠陥を検出 | |
表層部欠陥 | 渦流探傷試験(ET: Eddy Current Testing) | 導電性のある材料に対して渦電流を発生させ、表層部の欠陥を検出 |
磁粉探傷試験(MT: Magnetic Particle Testing) | 磁性体の表面に磁粉を散布し、表面近くの欠陥を検出 | |
表面開口欠陥 | 浸透探傷(PT: Penetrant Testing) | 浸透液を使用し、表面に開口している欠陥を検出 |
外観検査に強いAI会社の選定・紹介を行います
今年度AI相談急増中!紹介実績1,000件超え!
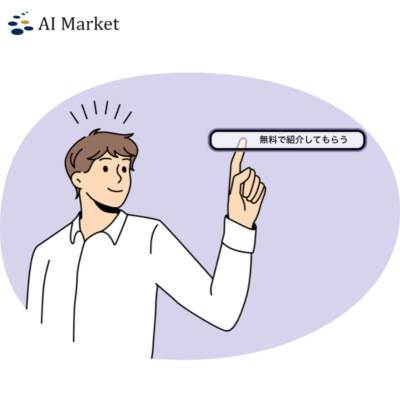
・ご相談からご紹介まで完全無料
・貴社に最適な会社に手間なく出会える
・AIのプロが貴社の代わりに数社選定
・お客様満足度96.8%超
完全無料・最短1日でご紹介 外観検査に強いAI会社選定を依頼する
非破壊検査の4つのメリット
非破壊検査には、さまざまなメリットがあり、製造業やインフラ管理の現場で広く利用されています。以下では、非破壊検査のメリットを紹介します。
対象物の損傷がない
非破壊検査の大きなメリットは、対象物を破壊せずに検査ができることです。検査後も製品や部材をそのまま使用でき、完成した製品を検査する際には製造・材料コストを減らせます。
特に高価な製品や特殊な部品では、検査のために余分に製造する必要がなくなるため、大きなコストダウンにつながります。
内部の欠陥を発見できる
非破壊検査は、人が目視で確認できないインフラ内部の欠陥を早期に発見し、重大な事故や故障のリスク軽減に大きく貢献します。放射線透過試験や超音波探傷試験などの高度な技術を用いることで、目視では見逃してしまうような内部の欠陥も高精度で検出できます。
製品や設備の形状や表面の状態、寸法を検査する外観検査と異なり、内部の欠陥を識別する必要のある非破壊検査は、インフラの劣化状況を確認するうえで重要な技術です。例えば、橋梁やトンネル、発電所など社会基盤を支える重要なインフラの定期検査に活用されています。
全数検査が可能
非破壊検査は対象物を破壊しないため、全数検査が可能です。これにより、不良品の流出を防ぎ、製品の品質管理が徹底されます。
目視検査と比べて検査精度が高い
非破壊検査は超音波や放射線などの技術を用いることで、目視では確認できない内部の欠陥や劣化も高精度に検出可能です。例えば、鉄鋼製品の内部に発生した微細な亀裂や溶接部分の不良など、肉眼では見つけにくい欠陥を正確に検出できます。
そのため非破壊検査を利用することで、製品の品質向上だけではなく、重大な故障や事故を未然に防ぐことも期待できます。
非破壊検査の5つのデメリット
一方、非破壊検査にはいくつかのデメリットも存在し、導入や運用には注意が必要です。以下では、非破壊検査のデメリットについて紹介します。
高度な技術が求められる
非破壊検査の精度と信頼性を確保するためには、高度な専門知識を持った従業員が必要です。特に検査機器の操作やデータの解析には高度なスキルが求められるため、従業員の育成や教育が重要です。
また、各検査手法ごとに特定の技術や知識が求められ、検査を実施する技術者の育成には多くの時間と労力がかかります。例えば、超音波探傷試験や放射線透過試験などは、専門的なトレーニングと経験が必要です。
熟練したスキルを持つ技術者が不足している現場では、検査の質にばらつきが生じます。そのため、熟練従業員の検査ノウハウやスキルを標準化する仕組み作りが必要です。
高価な機器が必要な場合がある
非破壊検査には高価な装置が必要となることがあります。特に放射線透過試験や超音波探傷試験の装置は高価であり、高度な機能や精度を求める場合にはさらにコストがかかります。
また、これらの装置の維持管理にも費用がかかります。
大量のデータ分析に時間がかかることがある
非破壊検査では膨大なデータを分析する必要があるため、十分な時間とリソースが必要です。特に以下のような検査では、データの解析に多くの時間を要します。
- 大型の構造物
- 複雑な製品
- 高い精度を求められる
- 微小なサイズの欠陥
解析に時間がかかる場合には生産や設備の稼働がストップし、大きな損失が生じるリスクもあります。そのため、大量のデータ分析を効率良く処理できるシステム導入が欠かせません。
検出できる欠陥の種類や大きさに制限がある場合がある
非破壊検査は万能ではなく、検出できる欠陥の種類や大きさに制限があります。例えば、磁粉探傷試験は強磁性材料にしか適用できず、非磁性体には使用できません。また、表面のきずは検査できても内部のきずは検出できない場合もあります。
欠陥の誤検出や見落としのリスクがある
非破壊検査は高度な分析力が求められるため、検査経験の浅い従業員が実施する場合には誤検出のリスクが高まります。また、直接製品や設備を壊して内部の劣化状況を確認できる「破壊検査」に比べると、非破壊検査はデータを通じて間接的にしか確認できないため、劣化を見落としてしまう可能性も高まります。
そのため、従業員の経験差を埋められる「ナレッジマネジメントツール」や劣化の見落としをなくせる「検出システム」の導入が必要です。
外観検査に強いAI会社の選定・紹介を行います
今年度AI相談急増中!紹介実績1,000件超え!
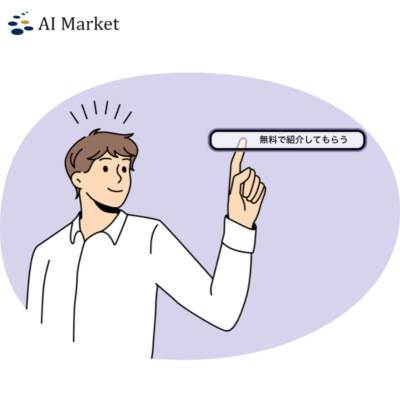
・ご相談からご紹介まで完全無料
・貴社に最適な会社に手間なく出会える
・AIのプロが貴社の代わりに数社選定
・お客様満足度96.8%超
完全無料・最短1日でご紹介 外観検査に強いAI会社選定を依頼する
AIを活用した非破壊検査の仕組み
AIの画像処理技術やデータ分析技術の高度化に伴い、従来の非破壊検査では検出できなかった微細な欠陥もスムーズに検出できるようになりつつあります。そのため、AIは従来の非破壊検査に対して、より効率と精度を向上できる技術として期待されています。
AI非破壊検査における高精度な欠陥検出の仕組みは、主に以下のような要素で構成されています。
AI非破壊検査に必要な要素 | 要素の説明 |
---|---|
高性能なセンサー技術 | 超音波探傷やX線などの非破壊検査技術を用いて、検査対象の内部構造を可視化します。 |
大量の学習データ | 1回の検査で数百万枚にも及ぶ画像データを収集します。これにより、微細な欠陥も見逃さない高解像度のデータセットを構築できます。 |
ディープラーニングで学習 | 大量の学習データから欠陥の特徴を学習し、人間の目では見逃しやすい微細な異常も検出できます。 従来の画像処理技術やデータ分析技術では検出が難しかった複雑な欠陥パターンもAIを活用することで高精度に検出できるようになります。 |
画像認識モデル・データ分析モデル | 大量のデータを短時間で処理することが可能になります |
継続的な学習と改善 | 検査結果のフィードバックを基に、AIモデルを継続的に学習・改善する |
人間の専門知識との融合 | AIの判断結果を人間の専門家がレビューし、最終的な判断を下すハイブリッドアプローチも採用されています。これにより、より信頼性の高い検査が可能になります。 |
このように、AI非破壊検査は高性能なセンサー技術、大量のデータ、ディープラーニング、高速処理能力を組み合わせることで、従来の手法よりも高精度かつ効率的な欠陥検出を実現しています。さらに、継続的な学習と人間の専門知識との融合により、検査の信頼性と柔軟性を高めています。
関連記事:「画像認識とは?種類・活用方法・企業での導入ステップ・注意点を徹底解説!」
AIを活用した非破壊検査の4つの特徴
以下では、AIの非破壊検査の特徴を詳しく紹介します。
高いデータ処理能力
AIは大量の検査データを高速かつ正確に処理する能力を持っています。大量の画像や波形データを短時間で分析可能です。これにより、従来の手法では見逃されがちな微細な欠陥を迅速に検出できます。
AIのアルゴリズムは、画像やセンサーから得られる膨大なデータをリアルタイムで解析し、欠陥の有無を判断します。
予測メンテナンス
AIの非破壊検査では過去の劣化パターンから未知の設備故障や異常予測など予測メンテナンスに活用できます。これにより、効率的な保守管理が可能となり、設備のダウンタイムを最小限に抑えることができます。突発的な故障を減らせますので、設備の稼働率を向上させることが可能です。
AIによる予測メンテナンスは、長期的なデータ蓄積によってさらに精度が向上し、より信頼性の高いメンテナンス計画を立てることができます。最適なメンテナンスのタイミングを提案できれば、コスト削減にもつながるでしょう。
関連記事:「予知保全とは?予防保全・事後保全・予兆保全との違い、メリット・デメリットを解説」
高精度な欠陥検出
AI技術は、高精度で欠陥を検出する能力があります。特にディープラーニング技術を用いることで、複雑なパターン認識が可能となり、人間の目視では困難な微細な欠陥も自動的に検出できます。
また、一貫性のある判断基準で検査を行うことができ、人間の専門家と同等以上の精度で欠陥を検出できます。これにより、製品の品質管理や安全性向上に大きく貢献しています。
自動化と効率化
AIを活用することで非破壊検査プロセスの自動化が進み、人手による作業を減らし、人的ミスを低減できます。それにより、検査員の負担を軽減し、より高度な判断業務に集中できるようになります。
また、検査データが蓄積されることでよりAIの劣化予測に対する学習が進み、長期的に活用することで検査精度がさらに向上します。
外観検査に強いAI会社の選定・紹介を行います
今年度AI相談急増中!紹介実績1,000件超え!
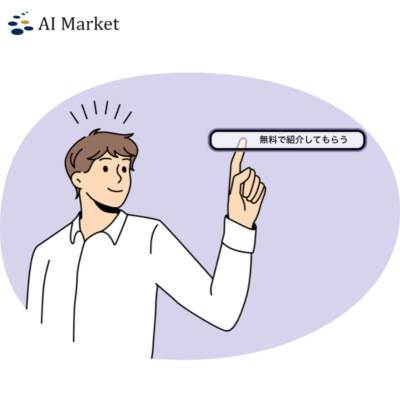
・ご相談からご紹介まで完全無料
・貴社に最適な会社に手間なく出会える
・AIのプロが貴社の代わりに数社選定
・お客様満足度96.8%超
完全無料・最短1日でご紹介 外観検査に強いAI会社選定を依頼する
AIの非破壊検査の活用例
AIの非破壊検査は積極的に開発が進められており、以下では、AIの非破壊検査の活用例を紹介します。
【野村総合研究所】交通インフラの非破壊検査の調査・点検データを自動解析
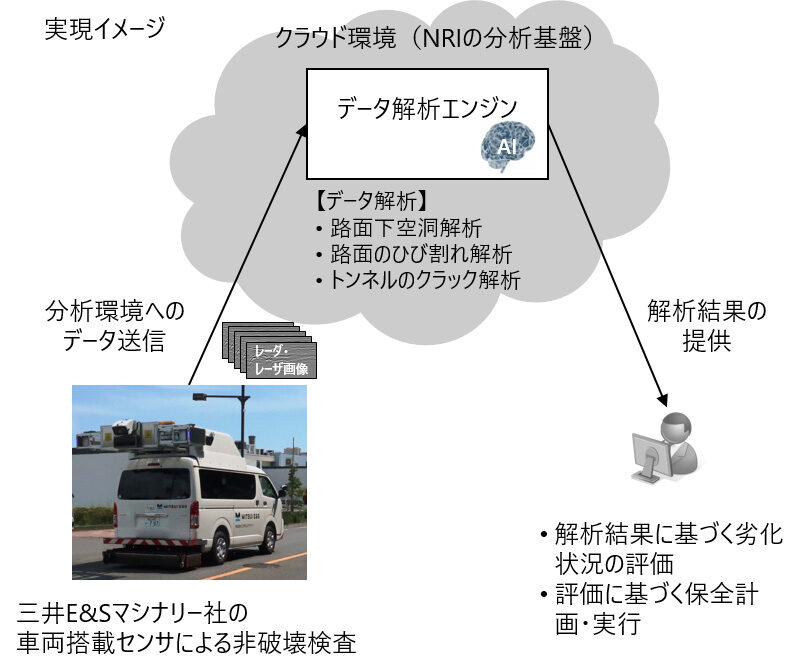
株式会社野村総合研究所は、非破壊検査で得た道路・トンネル等の交通インフラ調査・点検データをクラウド上で自動解析する仕組みを構築しました。この新しい仕組みにより、大量の非破壊検査データを解析する際の負担を軽減するほかに、技術者の経験差による解析結果のばらつきが平準化され、点検データの品質向上が期待できます。
実際に路面下空洞調査では、レーダーとレーザーで収集したデータをこのAIに適用し、レーダー解析画像から路面下空洞を自動検出し、レーザー画像から路面にあるひび割れの自動抽出・描画が可能になりました。
これにより、レーダー解析では空洞判定・抽出に7割、レーザー画像解析ではひび割れ抽出に9割の時間を短縮し、迅速な解析結果の提供を実現しています。
またトンネル点検では、トンネル撮影車で取得した高精細画像をAIで解析し、幅0.2ミリまでのクラックを自動検出できるようになりました。
【Laboro.AI/非破壊検査株式会社】ボイラーの検査データから損傷個所を自動検出
株式会社Laboro.AIは、ボイラーなどの熱交換器の強磁性伝熱管を対象とした非破壊検査に対してAIを活用しています。
非破壊検査株式会社が特許を保有する検査技術『強磁性チューブ渦電流探傷技術(FTECT:エフテクト)』にAIを適用し、検査データから「渦電流探傷試験技術」を用いて減肉などの損傷箇所を自動抽出します。
従来、検査データは人の目で波形を確認して損傷箇所を特定しており、解析には高い専門知識と多くの時間を要していました。
そこで損傷箇所特定AIソリューションを導入することで、データ解析の自動化と省力化の実現を目指しています。今後このAIソリューションを活用することで、データ解析量が従来比で約60%増加すると見込まれています。
【三菱電機】金属表面を撮影するだけで内部損傷を推定
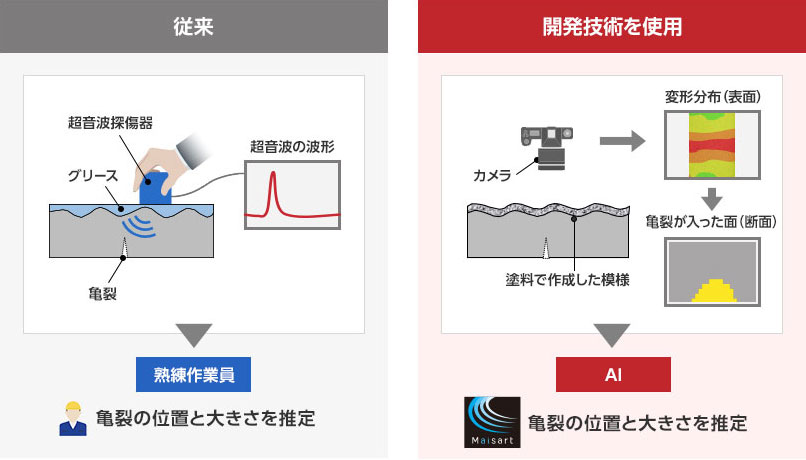
三菱電機は東京工業大学との共同研究で、金属表面の微小変形から内部の亀裂の位置と大きさを推定するAIを開発しました。このAIを用いることで、金属表面を撮影するだけで非破壊検査が可能となり、電力機器の保守点検に用いることで、熟練作業者の不足解消に貢献することが期待されています。
従来、電力機器の保守点検作業では、熟練作業者が幅約1cmで超音波探傷器を走査させて得た計測データから、内部の亀裂を推定していました。
開発されたAIは金属表面の画像データのみで、超音波探傷器を用いた非破壊検査と同等の亀裂推定精度を実現します。
【キヤノンITソリューションズ株式会社】CT装置画像にある物体内部の微小な欠陥を検出
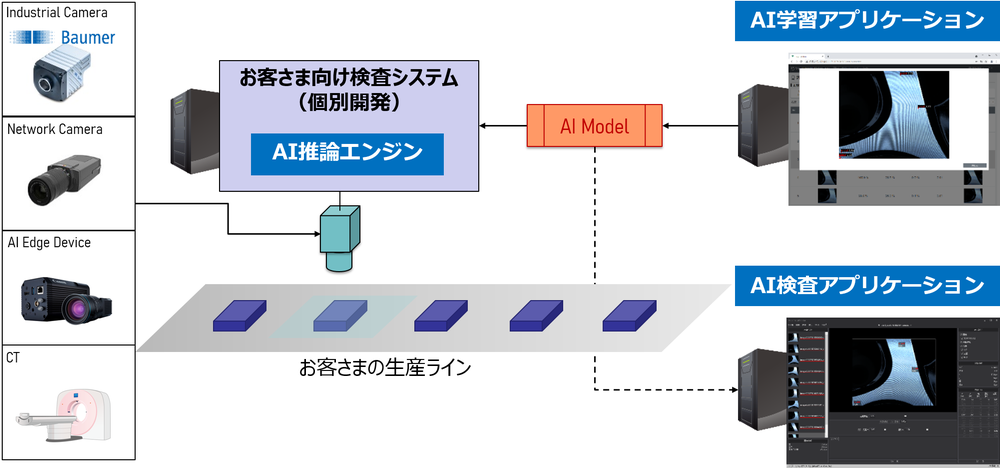
キヤノンITソリューションズ株式会社は、AIを用いた非破壊検査システム「Visual Insight Station」を開発しました。このAIシステムは、CT装置で撮像した物体内部の微小な欠陥を自動検出でき、非破壊検査の自動化と精度向上を実現します。
このシステムの特徴は、導入後に顧客自身でAIの追加学習やメンテナンスが可能な点です。この機能により、検査対象の追加や検査環境の変化に合わせて柔軟にAIを最適化でき、常に高い精度を維持できます。
このAIシステムは、長期的にAIの認識率を高く保つことができ、検査の効率化と品質向上に貢献できるシステムとして期待されています。
【東京エレクトロン デバイス】ガラス製品のAI欠陥検査で99.8%の判別精度を実現
東京エレクトロン デバイス株式会社が支援する、あるディスプレイパネルの製造プロセスでは、ガラス表面の傷検査や液晶の偏光板フィルムの不良検査など、さまざまな検査が行われます。
検査対象の製品は、出荷時にガラス面に傷がつかないように保護フィルムで覆われていますが、従来のルールベースによる画像処理だけでは、外部の保護フィルムの汚れと内部の偏光板フィルムの欠陥を正確に区別することが困難でした。
そこで、約5,000枚〜10,000枚にのぼる膨大な画像データをAIに学習させることで、精度の向上を図りました。導入の結果、検査システムは99.8%の高い正解率で欠陥を判別できるようになり、従来の人的検査に比べて大幅なコスト削減と効率化を実現しています。
関連記事:「ガラス外観検査とは?AI活用のメリット・事例・導入手順を徹底解説!」
非破壊検査についてよくある質問まとめ
- AIを活用した非破壊検査システムはどのような産業で利用されていますか?
AIを活用した非破壊検査システムは、自動車・航空宇宙・エネルギー・建設・製造業など、多岐にわたる産業で利用されています。特に、安全性が重視されるインフラ分野や精密な品質管理が必要な製造現場において、AIの導入が進んでいます。
- AIによる非破壊検査は、従来の方法と比べてどのようなメリットがありますか?
AIによる非破壊検査は、検査行程の自動化や高精度な欠陥検出、リアルタイムのデータ解析などにより、従来法と比べて検査の効率化と精度向上が期待できます。また、ヒューマンエラーを削減し、予測メンテナンスが可能になるため、コスト削減や安全性の向上に貢献します。
まとめ
非破壊検査は、製品やインフラの安全性を確認するための重要な技術です。従来の目視検査では見つけにくい内部の欠陥を破壊することなく検出でき、製品の品質向上やコスト削減に貢献しています。
一方、非破壊検査には高度な技術と専門知識が必要で、データ解析に時間がかかるデメリットもあります。
そこで、近年注目を集めるのがAIを活用した非破壊検査です。AIを活用することで、検査プロセスが自動化され、より迅速かつ正確に欠陥を検出でき、従業員の負担軽減やヒューマンエラーの削減が期待されます。
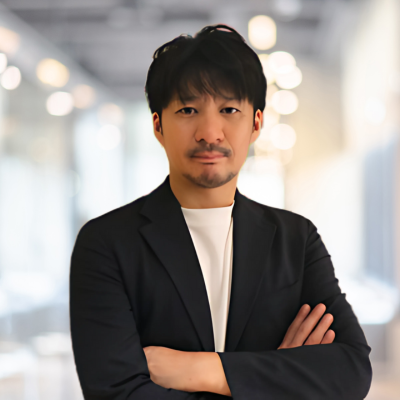
AI Market 運営、BizTech株式会社 代表取締役|2021年にサービス提供を開始したAI Marketのコンサルタントとしても、お客様に寄り添いながら、お客様の課題ヒアリングや企業のご紹介を実施しています。これまでにLLM・RAGを始め、画像認識、データ分析等、1,000件を超える様々なAI導入相談に対応。AI Marketの記事では、AIに関する情報をわかりやすくお伝えしています。
AI Market 公式𝕏:@AIMarket_jp
Youtubeチャンネル:@aimarket_channel
TikTok:@aimarket_jp
運営会社:BizTech株式会社
掲載記事に関するご意見・ご相談はこちら:ai-market-contents@biz-t.jp
