製造業でデジタルツインはどう活きる?メリット・6つの活用事例を徹底解説!
最終更新日:2025年08月20日
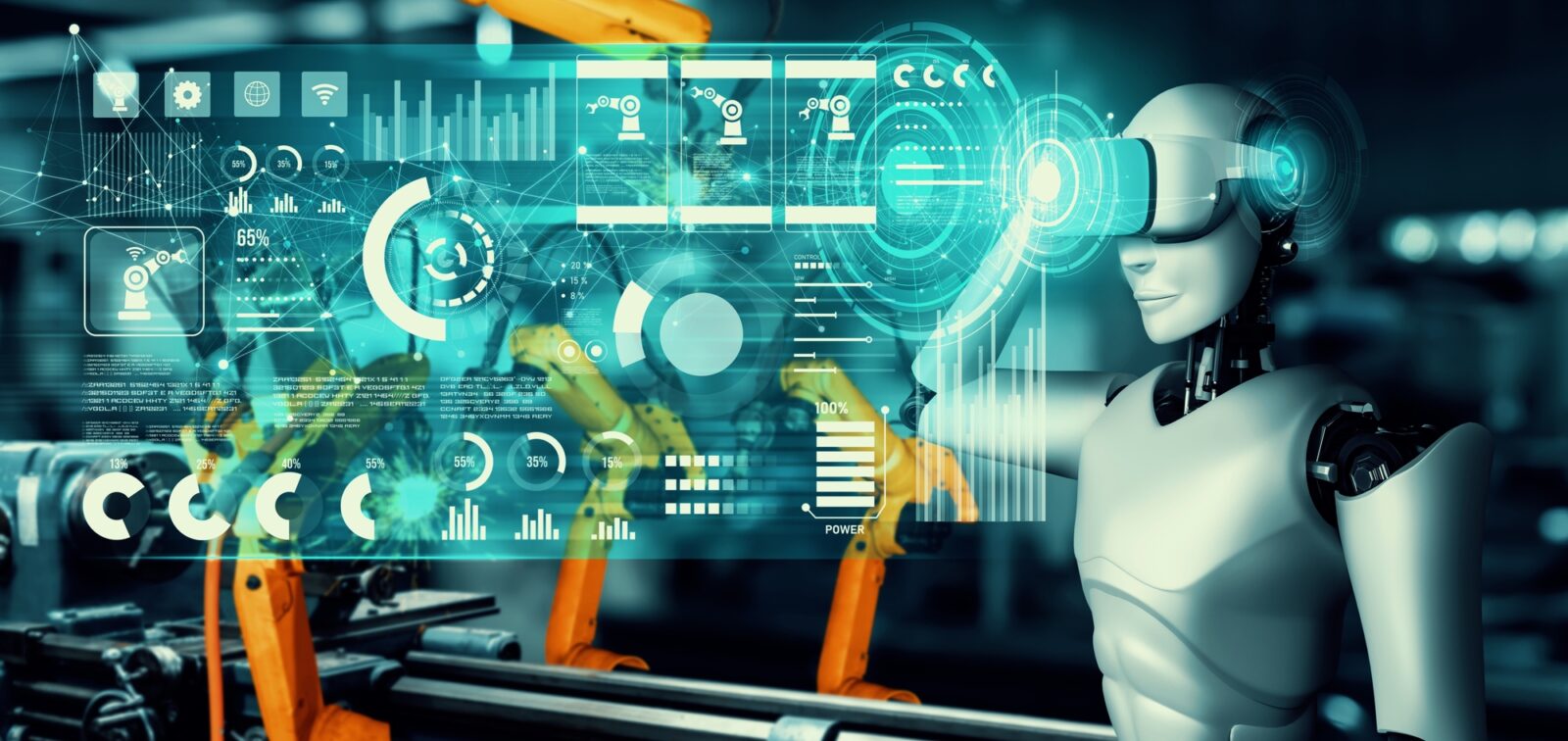
「製造業でデジタルツインが普及しているのはなぜ?」
「製造業でのデジタルツインの活用事例は?」
製造業では欠かせないツールになりつつある「デジタルツイン」。大企業は続々と導入しているけれど、高額な初期投資をしてまで導入するメリットはあるのか?と疑問に感じている方も多いのではないでしょうか。
本記事では、デジタルツインのメリット・活用事例を製造業に特化して解説します。製造業でデジタルツインがどのように活用されている事例を紹介していますので、自社に取り入れられる点を具体的なプランと共に確認できます。
製造業だけにとどまらないデジタルツインの可能性、AIが果たす重要な役割についてはこちらの記事で特集していますのでご覧ください。
製造業でのAIシステム開発に強い開発会社をお探しの方は、こちらの記事を参考にできます。
製造業に強いAI会社の選定・紹介を行います
今年度AI相談急増中!紹介実績1,000件超え!
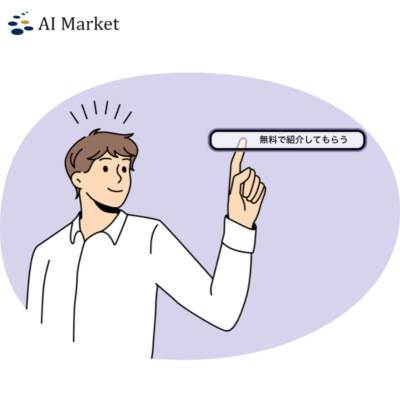
・ご相談からご紹介まで完全無料
・貴社に最適な会社に手間なく出会える
・AIのプロが貴社の代わりに数社選定
・お客様満足度96.8%超
完全無料・最短1日でご紹介 製造業に強いAI会社選定を依頼する
目次
製造業でデジタルツインはどのように使われている?
デジタルツインは、現実世界から得た情報を基に作り上げたデジタル仮想空間を指します。全くの仮想世界ではなく、あくまでも現実世界を模して造られていることがポイントです。デジタルで作り上げた双子(ツイン)なのでデジタルツインと呼ばれています。
製造業では、デジタルツインで「機器・部品の状況把握」「デジタル上で工場を試運転する」といった活用方法が既に多く開発されています。デジタルツインを活用しやすい業種のため、多くの製造業者が早い段階から導入しています。
デジタルツイン・シミュレーション・メタバースの違い
デジタルツインと混同されやすいシミュレーションやメタバースとの大きな違いは、以下の表のように「現実世界とリンクしているか」と「デジタルであるか」の2つです。
現実世界とのリンク | デジタルであるか | |
---|---|---|
デジタルツイン | 〇 | 〇 |
シミュレーション | △ | △ |
メタバース | × | 〇 |
デジタルツインはメタバースと異なり、現実世界とリンクしているデジタル空間です。加えて、シミュレーションと異なりリアルタイム性を持っているため、現実世界で起きたこともデジタル空間で確認できます。
さらに近年では、このデジタルツインにAI技術である「世界モデル」を組み合わせることで、単に現実を再現するだけでなく、「次に何が起こるか」という未来の状態を高精度で予測・シミュレーションする動きが加速しています。
デジタルツインとメタバースやシミュレーションの違い、AI、IoTなど用いられている技術についてはこちらの記事で詳しく解説しています。
製造業に強いAI会社の選定・紹介を行います
今年度AI相談急増中!紹介実績1,000件超え!
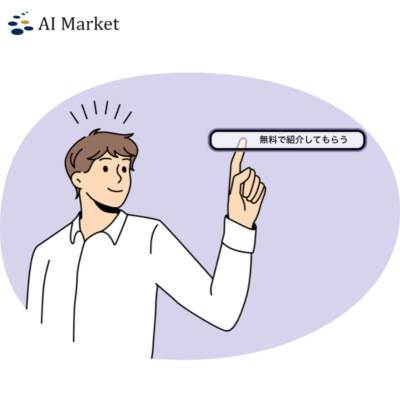
・ご相談からご紹介まで完全無料
・貴社に最適な会社に手間なく出会える
・AIのプロが貴社の代わりに数社選定
・お客様満足度96.8%超
完全無料・最短1日でご紹介 製造業に強いAI会社選定を依頼する
製造業におけるデジタルツイン5つのメリット
製造業でデジタルツインを活用するメリットは以下です。
1. 試作コストの削減
2. データ解析による品質向上
3. 予知保全が可能
4. 遠隔地でも現地の状況が確認できる
5. 技術伝承が効率的に行える
それぞれのメリットについて説明します。
試作コストの削減
デジタルツインには、CAEという「コンピューター上で試作や実験を行う」システムがあります。CAEを使えば、デジタル上で試作することができるため、試作にかかるコストや時間を大幅に削減することが可能です。
さらに、試験回数の上限がないため、満足のいく商品になるまで何度でも試作を重ねることができます。現実世界ではコストや安全確保のために長期の準備をかけて、一発勝負でしか行えないような試作品テストを何度も低コストで再現可能です。コストを抑えられるうえに、効率よく商品開発することが可能になります。
データ解析による品質向上
デジタルツインでは、IoTが人の目で見ることができない情報を収集してAIが高度な解析をしてくれるため、より詳細なデータを得ることができます。
それにより、商品に悪影響を与えている工程や機器の特定が容易になり、不良品の数を減らすことが可能です。
予知保全が可能
デジタルツインでは、IoTの監視とAIによるデータ解析により部品の故障・劣化を予測できるため、故障前に部品を交換する「予知保全」が可能です。
早期にデジタルツインを導入することで、蓄積データから工場ごとの特徴を掴んでイレギュラーな故障を予測することもできます。工場を正常に動かし続けることができるので、利益を上げることにつながります。
こちらで、AIを活用した予知保全のメリットと導入方法について詳しく解説していますのでご覧ください。
遠隔地でも現地の状況が確認できる
通信端末でデジタルツインを見ることができるので、僻地や遠隔地の状況把握をどこでも行うことができます。さらに、AR・VRを使えば現地の様子をリアルに知ることができるため、質を落とすことなく、現地視察や出張にかかる時間を短縮できます。また、現地に留まる必要がないため、優秀な人材に複数の事業所を担当してもらうことも可能です。
技術伝承が効率的に行える
デジタルツインでは、作業員の手元をどこからでも確認することができるため、遠隔地からの技術伝承が可能です。さらに、AIを用いれば作業の質を数値化できるため、どの作業を改善すればよいのかを明確にすることができます。
また、AR・VRを用いてデジタルツイン空間に入り込み、模擬作業を行うことも可能。現場に出られない新人の研修も、よりリアルな環境で行い、AIによる詳細なフィードバックを得ることができるので、作業の質をより効率的に上げることができます。
関連記事:「技能伝承でのAI活用は?継承が進まない原因やAIを導入するメリット、活用事例を徹底解説!」
製造業でのデジタルツイン活用事例6選
デジタルツインを実際に導入している事例をご紹介します。
- ベストプラクティスをデジタルツイン工場でテスト(富士通)
- VRでのバーチャル作業トレーニング(シーメンス)
- 高度なトレースによるメガリコール予防(日立)
- 蓄積データによる予知保全(ダイキン)
- 遠隔地からの指導による技術伝承(旭化成)
- デジタルツインでMaaSのシミュレーション(デンソー)
それぞれの事例について説明します。
ベストプラクティスをデジタルツイン工場でテスト(富士通)
富士通は、デジタルツイン空間に世界中の自社工場を再現し、詳細に把握・監視する仕組みを取っています。これにより、工場の横断的な分析が可能になり、どの工場のどの部門が優れているかを可視化できるようになりました。
部門ごとのベストプラクティス(最善例)を解析し、デジタルツイン空間で他工場に適用する取り組みもされています。適用後の方が良いとわかれば実際に取り入れ、工場の効率化を図ることができます。
上海の製造メーカーでは、富士通のデジタルツイン技術を使って実際の4階建ての組み立て工場をデジタルツインで作成しました。デジタルツイン上を歩きながら、それぞれの機械のステータスを細かく可視化したり、さまざまな視点でラインの状況をチェックできます。デジタルツインによって、リモートであっても設備の細かなメンテナンス指示を出すことが可能です。結果として不具合発生時のダウンタイムが大幅に短縮されますし、エンジニアの出張コストが不要になります。
VRでのバーチャル作業トレーニング(シーメンス)
シーメンスは、デジタルツイン空間に現場の作業スペースを作り出すことで、製品に関与することなく作業経験を積めるようにしています。VR・ARを活用することで、実際に作業しているかのような感覚で作業ができるのに加え、作業内容をデータ化することで人の目よりも細かい分析が可能。作業員のスキルアップが効率的に行えます。
また、製品に関与することなくトレーニングできるため、未熟な作業員を生産ラインに入れることなく研修することができます。ミスの原因もAIが細かく分析してくれるので、勘や慣れに頼った作業を減らすことができます。
高度なトレースによるメガリコール予防(日立)
日立は、デジタルツインを活用することで正確なトレースバック(製品から部品・材料ロットの特定)を可能にしているため、適正なリコール体制を取ることができ、メガリコールへの発展を予防しています。
また、デジタルツイン空間で生産ラインを一元管理することにより、部門間の連携も強化。部署ごとに管理されていたデータの一括管理ができるため、製品管理や品質評価を容易にしています。
蓄積データによる予知保全(ダイキン)
ダイキンは工場の保守にデジタルツインを活用しており、「止まらない工場」の実現を目指しています。2020年からデジタルツインで各工場のデータを集め、工場が止まる原因を調査・解析し、それらの情報を用いて予知保全に役立てるという計画です。
ダイキンでは、部品の劣化を時期を予知して事前に保全する「設備の予知保全」の他に、人的要因である作業の遅れも予知して対策を打つ「作業遅延の予知保全」も取り入れています。
早期から様々なデータを収集した結果、人やモノの動きのデジタル化ができ、生産シミュレーションや不具合の予知・予測が高い精度で行えるようになりました。これにより、安定した操業が可能になり、継続的な操業データ発掘とデータ分析が実現しています。顧客への高い価値提供が可能となりました。
遠隔地からの指導による技術伝承(旭化成)
旭化成は、作業場をデジタルツイン化して作業員の手元を確認できるようにすることで、遠隔地からの技術指導をできるようにしました。これにより、熟練技術者がどこにいても技術指導ができるようになり、技術伝承の効率化が実現。後継者不足問題を解決する糸口となりました。
その他、海外工場にもデジタルツインを導入し、日本からの操業支援も行う予定とのこと。これまで現地に駐在しなければいけなかった従業員をリモート対応させることができるため、従業員の負担軽減や経費削減などの効果も期待しているそうです。
デジタルツインでMaaSのシミュレーション(デンソー)
デンソーは、将来必ずメインストリームになると言われるMaaSを実現するために、多様な車両情報を一元管理、共有するためデジタルツインを活用しています。MaaSとは、バス、電車、タクシー、ライドシェア、シェアサイクルなどのあらゆる交通機関をシームレスに接続して、効率よく、便利に移動できることを目指すシステムです。
MaaSの仕組み、メリット・デメリットについてはこちらの記事で特集していますのでご覧ください。
デンソーは、IoTを活用して、現実世界の乗用車やバス、トラックなどが走行する状態をデジタルツインで忠実に再現する技術を開発しています。デジタルツインの都市空間で行われるシミュレーションをもとに、現実世界の交通システムにフィードバックし、安全で便利でエコフレンドリーな移動手段を構築しようとしています。デジタルツイン技術により、開発期間とコストが大幅に削減されるとのことです。
関連記事:「AIは自動車業界をどう変えている?活用方法・メリット・事例を徹底解説!」
製造業に強いAI会社の選定・紹介を行います
今年度AI相談急増中!紹介実績1,000件超え!
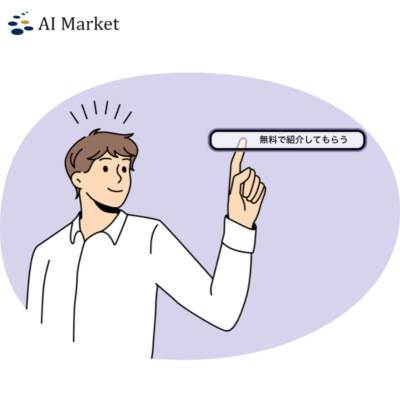
・ご相談からご紹介まで完全無料
・貴社に最適な会社に手間なく出会える
・AIのプロが貴社の代わりに数社選定
・お客様満足度96.8%超
完全無料・最短1日でご紹介 製造業に強いAI会社選定を依頼する
製造業でのデジタルツインについてよくある質問まとめ
- 製造業でのデジタルツイン活用のメリットは何ですか?
製造業でのデジタルツイン活用の主なメリットは以下の通りです。
- 試作コストの削減
- データ解析による品質向上
- 予知保全の実現
- 遠隔地からの状況確認
- 効率的な技術伝承
- デジタルツインの製造業での具体的な活用事例を教えてください。
製造業でのデジタルツイン活用事例には以下があります。
- ベストプラクティスのデジタルツイン工場でのテスト(富士通)
- VRを用いたバーチャル作業トレーニング(シーメンス)
- 高度なトレースによるメガリコール予防(日立)
- 蓄積データを用いた予知保全(ダイキン)
- 遠隔地からの指導による技術伝承(旭化成)
- MaaSのシミュレーション(デンソー)
- デジタルツインとシミュレーション、メタバースの違いは何ですか?
主な違いは以下の2点です。
- 現実世界とのリンク: デジタルツイン:あり シミュレーション:部分的にあり メタバース:なし
- デジタルであるか: デジタルツイン:はい シミュレーション:部分的に メタバース:はい
まとめ
製造業での活用が進んでいるデジタルツイン。技術伝承や品質管理を効率的に行うには欠かせないツールとなっています。比較的新しい技術ではあるものの、蓄積データを収集して精度を上げられるという特性から製造業では急速に普及が進んでいます。メーカーにとって大きな負担になってきた開発コスト、特に試作品コストを大幅に下げられるのは魅力です。競合企業より先に導入を検討してみてはいかがでしょうか。
デジタルツインの活用方法は無限にあり、工場の課題によって異なるため、適したツールを導入することが成功のカギとなります。と言っても、自社の環境にベストなシステム選定、開発業者選定にお悩みの方も多いのではないでしょうか?
高専、理系国立大学にて工学・農学を専攻後、AIを中心にテクノロジー調査や記事執筆を実施中。
AI開発会社やDXコンサルファームにて、AIのビジネス活用やテクノロジーの技術調査記事などを多数寄稿している。
