組立検査とは?種類・課題・外観検査AI活用のメリット・事例・導入手順を徹底解説!
最終更新日:2025年08月20日
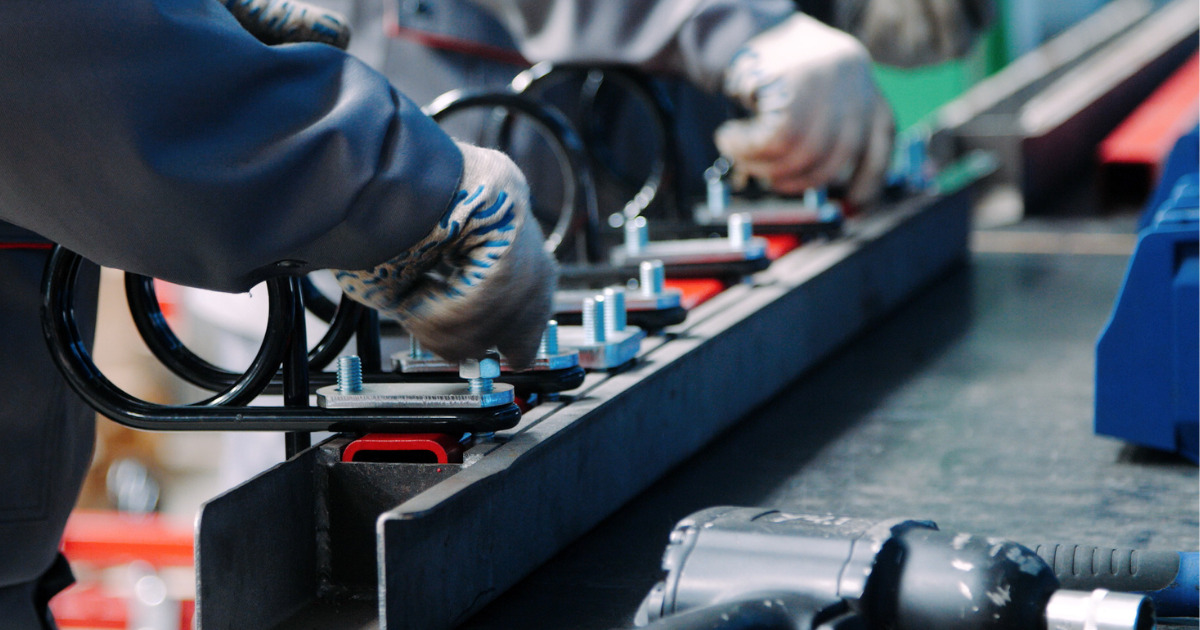
- 組立検査は製品品質の根幹を支えますが、製品の複雑化や人手不足により、検査難易度の上昇、精度維持、データ活用の面で課題
- AI(人工知能)導入は、高精度な判定による品質向上、属人化の解消、データ活用による迅速な工程改善に貢献
- 一方で、学習データ確保の難しさやコスト、未学習の不良への対応限界といった側面
- AIによる組立検査を成功させるには、解決したい課題の明確化、PoC(概念実証)による事前検証、対象や環境に適した機器選定が不可欠
組立検査は、製品の各部品が正しく組立られているかを確認し、最終製品の品質や安全性を左右する重要な工程です。熟練技術者による目視検査に頼るケースが多く、微細な不具合の見逃しや、検査結果にばらつきが生じるといった課題を抱えている現場も少なくありません。
AIを活用した外観検査システムは、従来の検査方法では捉えにくかった微細な欠陥も高精度に検出し、検査の一貫性と信頼性を向上させます。
この記事では、組立検査の基本から、AI技術を活用することでこれらの課題にどうアプローチできるかを具体的に解説します。見落としがちなデメリットや導入手順、実際の活用事例まで網羅的にご紹介しています。
外観検査に強いAI会社の選定・紹介を行います
今年度AI相談急増中!紹介実績1,000件超え!
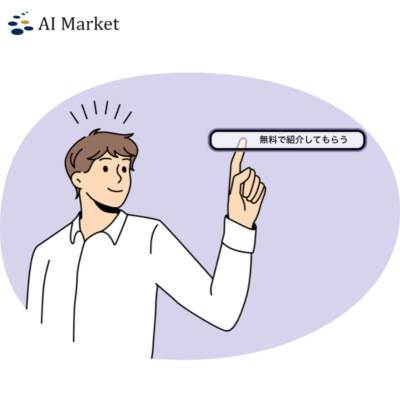
・ご相談からご紹介まで完全無料
・貴社に最適な会社に手間なく出会える
・AIのプロが貴社の代わりに数社選定
・お客様満足度96.8%超
完全無料・最短1日でご紹介 外観検査に強いAI会社選定を依頼する
製造業の外観検査に強いAI開発会社をご自分で選びたい場合はこちらで特集していますので併せてご覧ください。
目次
組立検査とは?
組立検査とは、製品(または半製品)や機器の各部品が正しく組立られているかを確認するための検査工程です。設計図や仕様書通りに正しく組み立てられているか、そして製品として期待される機能や性能を満たしているかを確認する、品質管理における重要なプロセスです。
組立検査では、以下のような製品の組立過程で発生し得るさまざまな欠陥を早期に発見します。
- 部品の取付ミス
- 部品間の位置ズレ
- 接合不良
- 微細な傷や変形といった外観上の問題
組立工程での不良が原因で製品の機能や安全性に影響を及ぼすリスクもあるため、細部にわたるチェックが不可欠です。
高精度な組立検査を通じて最終製品の品質向上と安全性を確保できれば、信頼性の高い製品を提供でき、顧客満足度の向上やブランドイメージの強化につながります。
主な組立検査の内容
組立検査の検査は、以下のように多岐にわたります。
- 外観検査: 部品の傷や変形、取付不良など、表面上の欠陥をチェック
- 寸法検査: 部品同士の位置や間隔、接合部の寸法が設計通りかを測定
- 機能検査・動作確認: 製品として正常に動作するか、電気的・機械的な機能が問題なく動くかを実際に動作させながら確認
- 締結状態検査:ネジやボルトが適切なトルクで締め付けられているか、嵌合(はめあい)部分がしっかりと組み合わさっているか
- 安全検査: 製品が使用中に安全性を確保できるか、過負荷状態や外部衝撃に対する耐性はあるかなど、製品が安全基準を満たしているかを検証
- カラーチェック:製品の色合いや塗装の均一性など、仕様に沿った美観が保たれているかを確認
- 耐圧検査:水圧や空気圧を用いて、製品の耐久性や耐圧性能を評価し、長期間の使用に耐える設計となっているかを判断
- 気密検査および漏れ検査:密閉状態が求められる製品に対して、気密性や漏れがないかを精密に測定
製品に合わせて必要な検査を実施します。
組立検査の主な手法
組立検査の主な手法は、以下です。
- 目視検査:熟練した検査員が直接見て欠陥をチェックする
- 測定器による検査:ノギス、マイクロメータ、トルクレンチ、高さゲージなどの測定器を用いて測定
- 検査治具の使用:専用の治具を使用
- 自動検査:カメラやセンサー、ロボットなどを組み合わせた自動化システム
- AI検査:主に画像認識AIを使用した、より高度な自動検査
多くの現場で取り入れられている手法が目視検査で、初期段階のチェックに有効です。ただし、検査員の技量に依存する度合いが高くなります。
自動検査は、短時間で大量の製品を高精度で検査する手法です。均一な検査品質が維持されるとともに、人的ミスの低減にもつながります。
AI検査は、複雑なパターンや従来の手法では見落としがちな微細な不良も高い精度で検出します。検査プロセスの自動化と効率化がさらに進み、品質管理レベルを一層向上できる点が大きなメリットです。
外観検査に強いAI会社の選定・紹介を行います
今年度AI相談急増中!紹介実績1,000件超え!
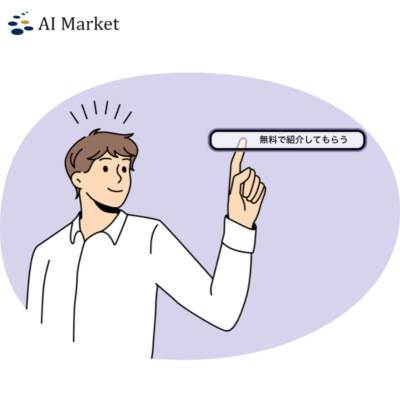
・ご相談からご紹介まで完全無料
・貴社に最適な会社に手間なく出会える
・AIのプロが貴社の代わりに数社選定
・お客様満足度96.8%超
完全無料・最短1日でご紹介 外観検査に強いAI会社選定を依頼する
組立検査が抱える課題
重要な役割を担う組立検査も、様々な課題を抱えています。組立検査が直面している主な課題について掘り下げてみましょう。
検査の難易度が高くなっている
スマートフォンや自動車部品のように、製品はますます小型化・複雑化・高機能化しています。これにより、検査すべき項目が増え、検査の難易度も格段に上がっています。
組立検査では、製品や機器の各部品が正確に配置され、接合されているかを厳密に確認する必要があります。例えば、微小なズレや微細な不具合であっても、最終製品の性能や安全性に直結するため、検査過程での見逃しは許されません。
また、現代の製品は機能やデザインの多様化・複雑化が進んでいるため、従来の単純な検査項目ではカバーしきれず、より多くの検査項目や複雑な基準が求められています。
検査基準の難化に伴い、組立検査では高度な技術や豊富な経験を必要とし、検査自体の難易度が高くなっています。
検査員の人手不足
組立検査では熟練検査員の高齢化、そして退職に伴い、人手不足が進み、検査工程における品質維持が難しくなっています。
また、複雑な検査基準のため、若手人材の育成・教育に時間がかかり、十分なスキルを持つ新しい検査員の確保が間に合っていない状況も人手不足を加速させている原因です。
細部にわたる目視チェックや精密な測定は、高い集中力と労力を必要とし、長時間の作業は肉体的・精神的負担を伴います。そのため、業界全体での人材育成と確保だけでなく、検査自動化などの技術的解決策の導入が急務と考えられています。
判定精度にばらつきが生じる
組立検査では、検査員個々の技術や経験、その日の体調や集中力により判定の精度にばらつきが発生することがあります。特に目視検査の場合は個人差が顕著で、微細な欠陥の判断基準が統一されないと同じ製品でも評価にムラが生じる恐れがあります。
色合い、手触り、異音など、数値化しにくい感覚的な検査は、特に個人差が出やすくなります。
こうした課題を解決するためには、検査基準の明確化や定期的な研修、さらには自動検査システムやAI技術の活用による客観的な評価手法の導入が重要となります。
検査データの活用不足
検査で得られた不良情報などのデータを収集・分析し、設計や前工程(組立工程自体)にフィードバックして品質改善につなげるループが十分に機能していない場合があります。データが記録されるだけで活用されていないケースも見られます。
関連記事:「AIは4M分析をどう変える?4Mごとの活用方法・メリット・事例・活用時の課題を徹底解説!」
AIを活用した組立検査のメリット
AIを組立検査に取り入れることで、検査品質やコスト面でメリットをもたらします。AIによる外観検査は、組立検査だけでなく、はんだ付けや溶接検査、半導体、ラベル、そしてガラス製品と言った製造業で不可欠な検査に活用されています。
AIを組立検査で活用するメリットについて、従来の外観検査システムや目視検査と比較しながら紹介します。
高精度な判定
画像認識AIは膨大な学習データを元にパターン認識を行い、従来の目視検査では見逃されがちな微細な部品の欠陥や形状の微妙なズレまで高精度に判定できます。
例えば、部品間の接合状態や表面の細かい傷などを判定できます。
物体検出アルゴリズムを使えば、画像や点群データの中から特定の部品や欠陥の位置を特定可能です。「部品が付いているか/いないか」「ネジが正しい位置にあるか」「異物が混入していないか」などを検出するのに使われます。
また、画像分類アルゴリズムで画像全体を見て、それが「良品」か「不良品」かを分類したり、不良品だった場合に「キズ」「汚れ」「欠け」など、どの種類の欠陥かを分類したりします。
人間では見逃しがちな微細なキズや汚れ、複雑なパターンの欠陥なども、AIは高い精度で検出可能です。
カメラが捉えた画像データだけでなく、3Dセンサーから得られる立体的な点群データも活用可能です。AIの導入により、不良品の混入リスクを低減し、製品全体の信頼性を高める効果が期待されます。
属人化の解消
AIの外観検査システムは、同一のアルゴリズムに基づいて一貫した判断を下すため、操作する従業員の経験やノウハウによらず同じ品質基準を維持できます。
定期的に検査データを追加、再学習を行うことで、最新の検査基準にも柔軟に対応可能です。
異常検知アルゴリズムを使って大量の「良品」データのみをAIに学習させることで、それらとパターンが異なるもの(=異常)を検出することもできます。事前にあらゆる種類の不良品データを準備する必要がないため、長年磨いたベテランの勘でしか見つけられなかったような発生頻度の低い不良を発見するのに有効です。
また、AIの外観検査システムの基準に基づいて判断を下す仕組みを取れば、熟練従業員が新人を一から教育するコストや時間を削減できるため、長期的な人材育成の効率向上につながります。
改善対応の迅速化
AI外観検査システムは、異常が検出された瞬間にアラートを発信する仕組みを構築できます。AIの分析機能とアラーム機能により、問題箇所の特定を迅速にでき、不良の原因究明や対策の実施を早められます。
さらに、検査結果のデータは自動で蓄積され、工程改善に活用できるため、品質向上のためのPDCAサイクルを加速することも可能です。不良発生の傾向を早期に掴み、原因を特定しやすくなり、設計や組立工程へ迅速にフィードバックして根本的な品質改善につなげることが可能です。
ライン全体の生産効率を向上させるだけでなく、製品の不良率低減にも大きく貢献します。
検査の標準化と継承
目視検査では、検査基準の解釈が検査員や日ごとに異なることが課題となりがちです。
一方、AIの外観検査システムは、プログラムされたルールや学習済みモデルに基づいて一律の基準で検査を実施するため、検査基準のばらつきを削減できます。
さらに、標準化されたデータを元に、製造工程全体の最適化や新たな品質管理基準の策定が可能となる効果も期待されます。
熟練検査員の判定結果を教師データとしてAIに学習させることで、その「目」や「判断基準」といった暗黙知を形式知化し、AIシステムとして再現・継承することができます。
外観検査に強いAI会社の選定・紹介を行います
今年度AI相談急増中!紹介実績1,000件超え!
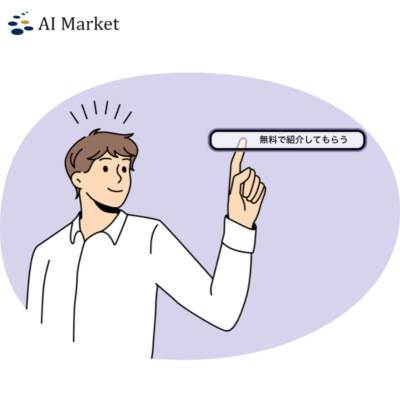
・ご相談からご紹介まで完全無料
・貴社に最適な会社に手間なく出会える
・AIのプロが貴社の代わりに数社選定
・お客様満足度96.8%超
完全無料・最短1日でご紹介 外観検査に強いAI会社選定を依頼する
AIによる組立検査のデメリット
AI技術を組み込んだ組立検査システムは高精度かつ効率的な検査を実現する一方で、いくつかデメリットも存在します。以下では、組立検査にAIを取り入れる際のデメリットを紹介します。
学習データの確保が難しい
高精度なAI外観検査を構築するためには、十分な量と質の高い学習データが不可欠です。
しかし、多くの現場では、検査に必要な詳細な画像データや多様な検査データが十分にそろっていない場合があります。特に、不良品データは出現率が低く、収集に時間がかかります。
また、データ収集には現場関係者の理解と協力が必要です。通常業務で忙しい中、データ収集作業を並行して行う必要があり、想定以上に時間を要することがあります。
特にディープラーニングの精度を高めるには、大量かつ質の高い学習データが不可欠です。特に、様々なパターンの「不良品」データを網羅的に収集することは困難な場合があります。
画像の撮影、データへのラベル付け(アノテーション)作業にも、多くの時間と労力がかかります。
保有している検査データからAIの要件に合うデータを確保できない場合は、データの加工処理や生成処理で補う方法が一つの手です。
稀な不良品の学習データ収集が困難
AIは基本的に「学習した範囲内」の事象しか正しく認識・判断できません。そのため、過去の事例に十分に含まれていない稀な不良品や未知のパターンに対しては適切な判断が難しい場合があります。
過去に例のない全く新しいタイプの不良品や極めて特殊な不具合が発生した際に、従来の人手による検査と比べて見逃しが生じるリスクがあります。
稀な不良品が生じるリスクに備えるためには、目視検査を補完的に行うことやAIモデル・データの更新が必要です。
他にも、正常データを学習することで、正常データ以外を検知するアプローチ(オートエンコーダー)も増えており、これにより稀な不良品への対象も可能となってきています。
高額な初期投資
高性能なカメラ、照明、画像処理を行うためのコンピュータ(GPU搭載など)、AIソフトウェアライセンス、システムインテグレーション費用など、導入には多額の初期コストがかかることがあります。
専門人材の必要性とコスト
AIモデルの構築、精度を維持するためのチューニング、システムの運用・保守には、AIやデータサイエンスに関する専門知識を持つ人材が必要です。社内に適任者がいない場合、外部の専門家への委託費用や、人材育成のためのコストが発生します。
組立検査でのAI活用事例
実際にAIを活用し、組立検査における属人化の解消や目視検査の自動化に成功している企業もあります。以下では、AIを活用した組立検査の事例を紹介します。
AIにより組立工程の作業ミスの見逃し防止(OKI)
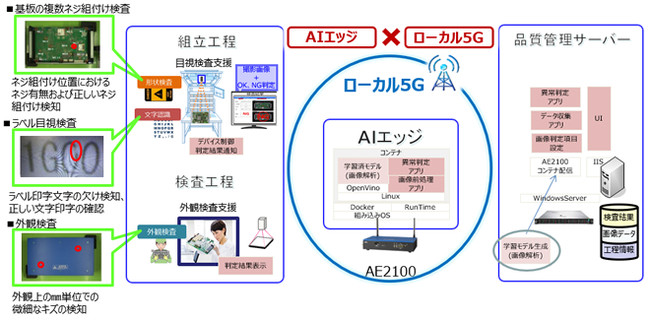
OKI(沖電気工業株式会社)は検査対象の部品・製品の映像データを熟練者の目と知(ノウハウ)に値するAI分析により目視検査を自動化する「外観異常判定システム」を開発しました。
本システムは、カメラで撮影された高精細な映像を、同社のAIエッジコンピューター「AE2100」が解析することで、外観異常をリアルタイムで判定し、即座に従業員に結果を通知します。また、判定結果を含む検査画像と製品情報などの各種証跡データは管理サーバーへ自動的に蓄積され、品質管理や工程分析に活用可能です。
実証実験では、高精細映像をローカル5Gネットワークで伝送し、AE2100で映像解析した結果、作業ミスの見逃しをゼロにできた上に、組立工程全体の作業時間を15%削減することに成功しました。
実証実験の結果から、従来の熟練者に依存する目視検査からの脱却と作業者の負荷軽減が期待されています。
製品の組立不良・組付け時に発生する不具合をリアルタイム判定(ブレインズテクノロジー)
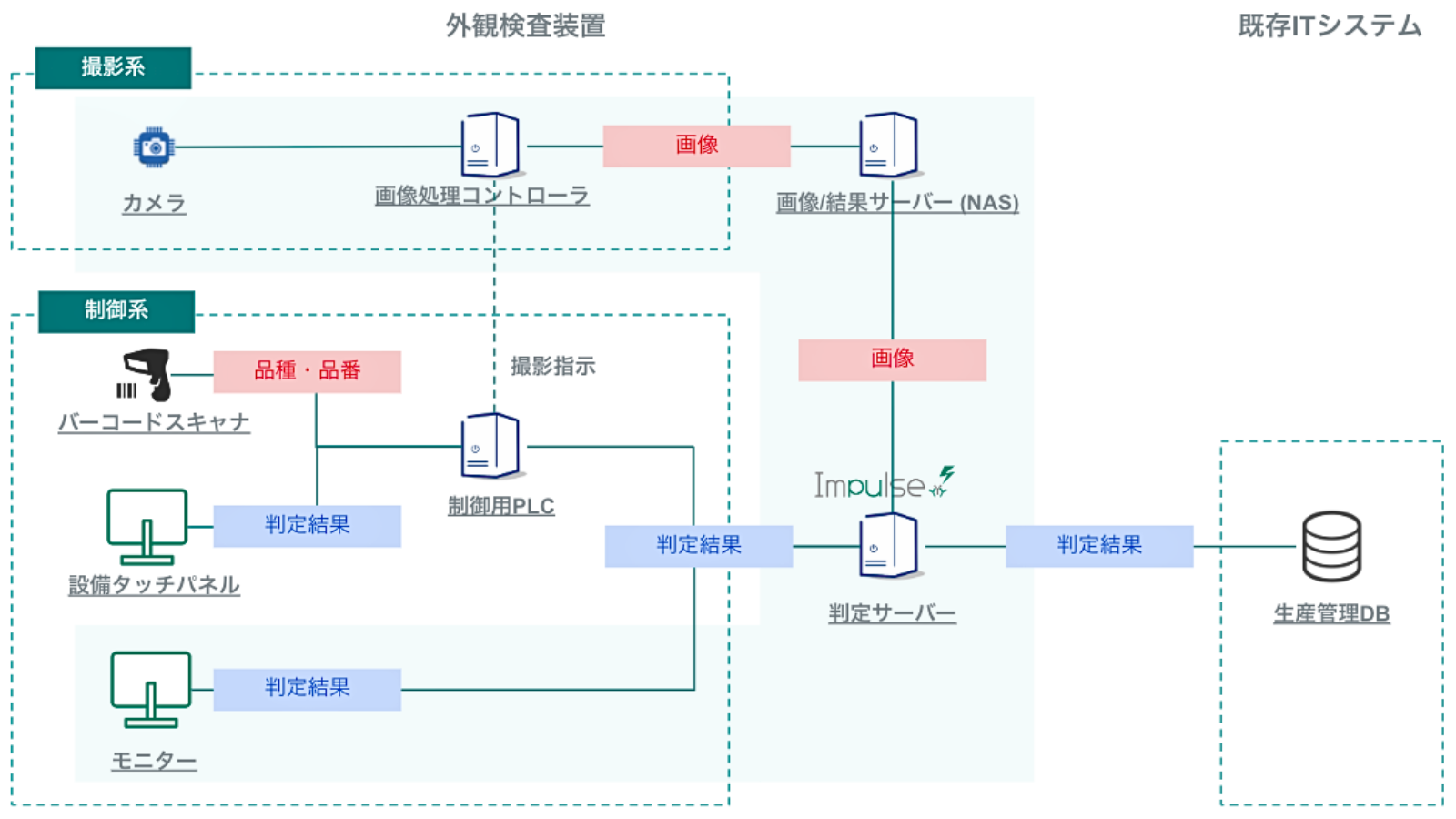
ブレインズテクノロジー株式会社のImpulseは、組立工程の目視検査の問題を解決するため、AIによる画像認識と分析技術を活用する組立不良分析システムです。組立不良を自動かつリアルタイムで判定します。
本システムは、組立時の動画データや組立製品の静止画データを取得し、良否判定を自動かつ高速に実行します。また、作業台で静止すると、自動撮影と推論処理が実施され、タブレット上に判定結果が即座に表示されます。
導入により、以下のようにさまざまな効果を得られました。
- 組立作業中に組み付けミスや部品の異常を識別でき、迅速な是正対応を推進
- 現場の運用性が向上し、人に依存しない運用が実現
- 検査データ蓄積により組付ミス防止が可能となり、トレーサビリティが向上
- 組付け間違いの流出を防ぎ、検査員の心理的負荷を軽減
- 未知の品番にも柔軟に対応でき、組み付けミス防止を実現
Impulseのシステムは、当事例以外にもエアバックの取付不良や配線の接続ミスなど、幅広い組立検査で活用されています。
部品組付けで高精度な判定精度を達成(サカタ製作所)
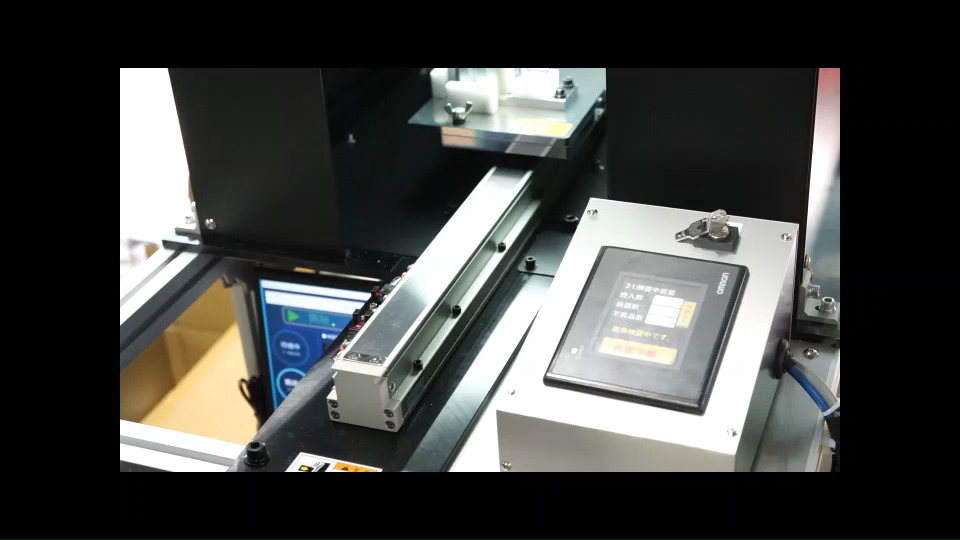
株式会社サカタ製作所では、ソーラーパネルの取付治具の製造・販売において、エンドユーザへの納品後に製品の組付け不良が発生する場合があり、信頼低下や取引の停止といったリスクを懸念していました。
従来、製品の組立状態は目視による検査で確認され、複数人によるチェック体制が敷かれていました。しかし、作業員の疲労や見間違いにより不良品を完全に検出することは困難でした。
品質管理の強化にはマンパワーだけでは限界が見えていた上に、今後検査員の確保が難しくなることも想定されるなか組立検査の自動化が求められる状況となりました。
そこで、株式会社BSNアイネットが提案したAI画像判定を用いた組立製品の検品システムの導入を決定しました。正常・異常の画像を学習させることで、以下のように複数の成果を得られました。
- ボルト長計測:画像処理技術により99%の判定精度を達成
- 部品組付け順誤り:不良品検知において99%の判定精度を達成
- 部品数が多いワーク:判定領域を区切りながら高精度な自動エラー検知を実現
今回の導入により、複数の部品を組付けた製品のエラーを検知できることが検証でき、今後は検査工程から梱包工程までの自動化が期待されています。
外観検査に強いAI会社の選定・紹介を行います
今年度AI相談急増中!紹介実績1,000件超え!
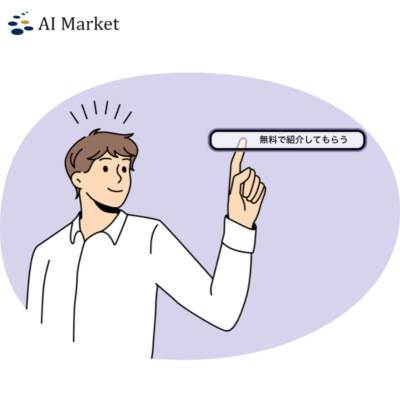
・ご相談からご紹介まで完全無料
・貴社に最適な会社に手間なく出会える
・AIのプロが貴社の代わりに数社選定
・お客様満足度96.8%超
完全無料・最短1日でご紹介 外観検査に強いAI会社選定を依頼する
AI組立検査の導入手順
組立検査にAIを導入する手順は、以下のとおりです。
組立検査付け検査におけるAI導入手順 | 詳細 |
---|---|
1.現状の確認 |
|
2.必要な機器とソフトウェアの選定 |
|
3.データ収集とラベリング(アノテーション) |
|
4.PoC(概念実証)による事前検証 |
|
5.AIシステムの訓練と検査精度の評価 |
|
6.本番環境へのデプロイ |
|
7.チームの研修とサポート体制の確立 |
|
関連記事:「AI開発の手順は?AIシステム構築の流れを徹底解説!」
組立検査についてよくある質問まとめ
- AI組立検査システムを導入するメリットは何ですか?
AIシステムは、熟練検査員に依存することなく、常に一貫した高精度の検査を実現します。これにより、検査漏れやばらつきを低減でき、トレーサビリティの向上、作業効率のアップ、そして作業者の負担軽減につながります。また、デジタルデータの蓄積による工程改善や迅速な是正対応も可能です。
- AI検査システムの導入による作業員の役割はどう変化しますか?
AIシステムの導入により、従来の検査作業は自動化されるため、作業員はシステムの運用管理やトラブル対応、データ分析など、より高度な業務にシフトすることが可能となります。これにより、作業者の負担軽減と同時に、スキルアップや新たな役割の創出が期待されます。
まとめ
組立検査は、製品や機器の品質保証につながる重要な検査プロセスです。従来の目視検査において検査精度のばらつきや作業負荷の増大が問題視される中、近年はAIを用いた外観検査技術が注目されています。
AIは、大量の学習データを基に微細な異常や部品の配置、接合状態を高精度に判定し、リアルタイムで検査結果を出力することで、検査漏れや過剰判定の低減を実現します。
AIの効果を最大限に引き出すためには、自社の状況に合わせた課題設定、十分な事前検証(PoC)、そして適切な運用体制の構築が欠かせません。特に、目的に合った学習データの準備や最適なAIモデルの選定、既存の生産システムとの連携などは、専門的な知見が求められる場面もあります。
もし、より具体的な導入計画の策定や技術的なアドバイスが必要だと感じられた場合は、経験豊富な専門家への相談を検討することをおすすめします。
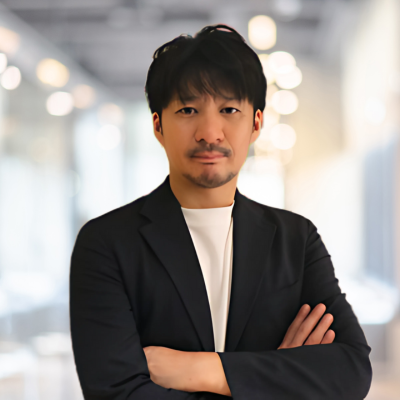
AI Market 運営、BizTech株式会社 代表取締役|2021年にサービス提供を開始したAI Marketのコンサルタントとしても、お客様に寄り添いながら、お客様の課題ヒアリングや企業のご紹介を実施しています。これまでにLLM・RAGを始め、画像認識、データ分析等、1,000件を超える様々なAI導入相談に対応。AI Marketの記事では、AIに関する情報をわかりやすくお伝えしています。
AI Market 公式𝕏:@AIMarket_jp
Youtubeチャンネル:@aimarket_channel
TikTok:@aimarket_jp
運営会社:BizTech株式会社
掲載記事に関するご意見・ご相談はこちら:ai-market-contents@biz-t.jp
