スマートファクトリー成功事例7選を紹介!失敗しないための注意点も徹底解説
最終更新日:2025年06月16日
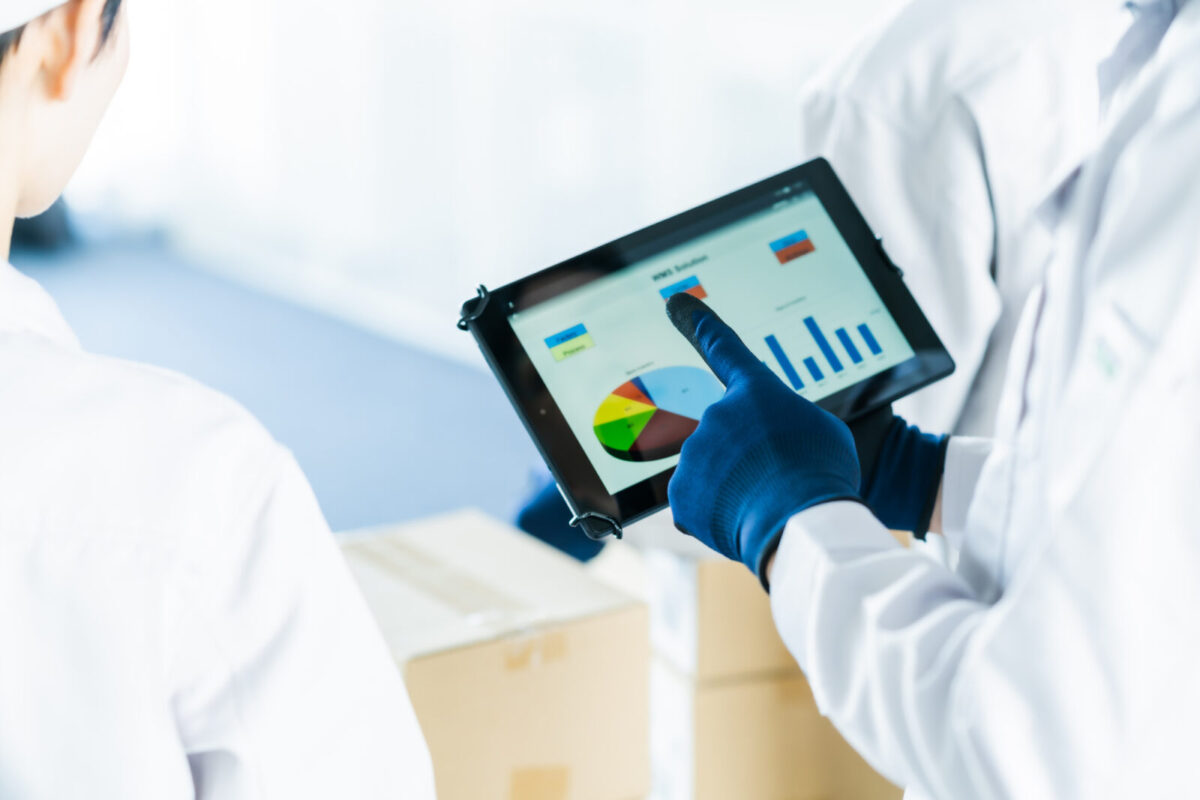
ドイツからの発信で「インダストリー4.0」が提唱されたことをきっかけに、日本でもIoTやAI技術を活用した「スマートファクトリー」が注目を集めています。
そこで、この記事では、
こちらでスマートファクトリーとは?導入事例・デメリットを詳しく説明しています。
AI Marketでは、
貴社に最適な会社に手間なく数日で出会えます
スマートファクトリー事例7選
スマートファクトリーの成功事例を紹介していきます。
IoTを活用し受注生産品の大量生産体制を整備(ダイキン)
ダイキンは、ビル用マルチエアコンを生産する新工場新工場を大阪・堺に稼働させました。さまざまなモノがインターネットにつながるIoTを活用し、顧客のニーズに応じた受注生産品を大量につくるマスカスタマイズ生産ができる体制を整えました。
この工場では、1本の生産ラインで異なる仕様の製品を流れ作業で組み立てることができます。生産ラインを流れるパレットに内蔵されたIDカードのなかの様々な情報を基に、生産ラインに作業指示が出され、異なる製品を組み立てることができます。
また、IDカードの情報を「工場IoTプロジェクトセンター」に集約し、生産状況の見える化を図るとともに分析を行って、設備の故障などの異常、生産の遅れを事前に検知する体制を整えています。こうしたスマートファクトリーにより、1つの生産ラインでマスカスタマイズ生産を可能にしています。
ロボットとICタグ導入で過去最高の生産歩留まりを達成(TOTO)
TOTO株式会社は、滋賀⼯場に最新鋭の技術の投資を行い、国内外全ての⼯場のモデルとなる先端の製造現場を作り上げました。生産ラインは混流⽣産で、流れる衛⽣陶器製品は品番が異なり、組み立て位置も毎回違ってきます。
管理の困難な混流生産でも、最新のセンサー技術を使い、⼨分の狂いもなく組み立て位置の違いを正確に識別し、迅速に位置を合わせるロボットを導入しました。
また、パレットにICタグを組み込んでおり、衛⽣陶器に貼り付けたバーコードに紐付けることで、⼀元管理を行っています。この ICタグとバーコードを読み取ることで、品番や⼯程で発⽣する各種ログ情報を呼び出すことが可能です。
製造ビッグデータとして⼯程管理や品質管理、出荷後のトレーサビリティなどに活⽤でき、過去最高の生産歩留まりを達成しました。
「匠の技」を数値化する(東洋製罐/ウイングアーク1st)
東洋製罐株式会社では、ウイングアーク1st株式会社の開発したシステムを活用して、製造ラインで働くベテラン社員のスキルを数値化・形式知化しました。
東洋製罐の製造ラインは、1つのラインに複数の工程があり、各工程に1~2人の担当者が付き、担当する工程の状況把握を行っていました。そのため、ライン全体の状況を俯瞰的に把握できていないことが課題でした。
また、担当者の高齢化も進み、経験の浅い社員でも品質を保持しながら効率的にラインを稼働できる体制づくりが求められていました。そこで製造ラインで働くベテラン社員の暗黙知となっているスキルを「見る(可視化)」「知る(通知)」「蓄える」ことでシステム化しました。
関連記事:「暗黙知とは?放置するリスク、形式知化の手法、AIで解決した企業事例を徹底解説」
スキルを数値化・形式知化することで、経験の浅い社員でも品質を保持しながらラインを稼働できる体制を構築しました。
具体的には、製造ラインで取得できる細かなデータを可視化できるITツールを活用しました。リアルタイムでライン全体の状況を把握、アラート機能を利用して、ラインの異常を素早く知らせる仕組みを構築しました。
また、一定の条件によりアラートが担当者のスマートフォンに通知される仕組みを自社開発し、担当者の負担を軽減することも可能です。
これにより、ライン全体の状況をリアルタイムで把握でき、少ない人数でも品質を保持しながらラインを稼働できるようになったのです。ベテラン担当者だけでなく、若手の担当者も適切に対処できる体制を作り上げることができました。
低コストでデータ収集の自動化・見える化(旭鉄⼯)
旭鉄工株式会社は、工場の改善を行う上で、現状把握とそれに伴う問題点の洗い出しのためにデータ収集の自動化・見える化を低コストで実現しました。具体的には、以下のような情報の収集・見える化を行いました。
- 各製造ラインの製造数量(時間あたり)
- 停止(時刻、長さ)
- サイクルタイム(製品1個を作る時間)
製品が1つできるたびに、シグナルタワーが点灯する機械なら光センサーを、安全扉の開閉など動きのある機械には磁気センサーを取り付けパルス信号を発生させます。市販の1つ50円程度の光センサーや、250円程度の磁気センサーと低コストなものを使用しています。
パルスの数で生産個数を、パルスの間隔でサイクルタイムを表すことで、作業時間のバラツキなどが分かるようになります。パルスの時間間隔が一定以上長くなれば、ラインが停止したと想定できます。こうした情報をクラウド経由で、責任者や担当者のスマートフォン、社内のモニターで見える化ができるようにしました。
製造ラインをスマートフォンで見えるようにしたことで、現場で状況を見ながら改善策を検討、実施していくことが可能になりました。同社の時間当たり出来高は、80ラインで平均34%、最大128%アップを実現しています。
旭鉄工では、自社で蓄積したIoTノウハウを元に、製造ラインのIoTデータモニタリングサービス提供やコンサルを行うi Smart Technologies(iSTC)を立ち上げました。
ダイセル式生産革新(ダイセル)
株式会社ダイセルの製造部門の改善手法「ダイセル式生産革新」は、その効果が着目され徐々に他社へも広がり、様々な製造業がその取り組みを導入しています。同社は、熟練工の大量定年退職する問題を迎えたことを契機に、熟練工のノウハウや技能を徹底的に見える化し、誰もが安心して作業が行える『人にやさしいモノづくり』 を目指しました。
しかし、人間はどうしてもミスしてしまうもので、仮にミスをしても安心して作業できる仕組みを模索し続けています。作業者の動作や設備・材料の状態を定量的に把握することが、製品の品質改善や生産性、安全性の向上を図る上で有効であることを突き止めました。
この結果をもとに、製造現場における作業員の逸脱動作やライン設備の動作不具合などの予兆を検出する「画像解析システム」を開発しました。システムは以下の要素で構成されています。
- 「人」に対応する人物動作解析
- 「設備」に対応する設備異常解析
- 「材料」に対応する溶接異常解析
3次元形状を取得できるカメラを用いて作業者の動作が規定した値を超えた場合や、設備や材料で、通常画像と比較し異常を検知した場合に、生産ラインの監督者に通知が送られる仕組みを構築しました。さらに生産工程に不適切な作業が発見された時は、シリアル単位で最終製品を追跡できるトレーサビリティも実現しました。
画像解析を活用した生産アシストシステムこれにより、ミスをしても安心して作業でき、製品の品質改善や生産性を向上させることに成功しました。
少数精鋭企業でも業務の見える化とベテラン社員の知識の共有(今野製作所)
株式会社今野製作所は、東京(営業と設計)・大阪(営業)・福島(製造)の3拠点、全社員数36名と少数精鋭でありながら、業務の見える化・IT化を実現しました。同社は以下のような課題がありました。
- 受注設計生産のベテランへ社員への仕事の集中・依存
- 世代交代や若手へのスキルの継承
- 作業時間が増加する一方で売上高が増加しない
これらを解決するために、まず1年かけて、受注→設計→生産→出荷までの「業務の見える化」の徹底を行いました。業務の見える化により、仕事の流れがどうなっているかを可視化することができました。
「業務の見える化」を徹底したことで、情報の流れを把握することができ、どの部分をIT化すべきかを把握することが可能となりました。次に、市販の業務アプリ構築クラウドサービスによる情報システムの構築を行いました。
この情報システムを活用することで、拠点間の状況をリアルタイムで連携するだけでなく、社員の知識や経験を共有することも可能になりました。こうした取り組みによって、同数の社員で特注品の売上高は2,000万円から9,000万円に増加しました。年間50件の設計提案は170件まで増加し、大幅な業務効率化を実現することができています。
AWSにおける4M分析のAI活用(Amazon)
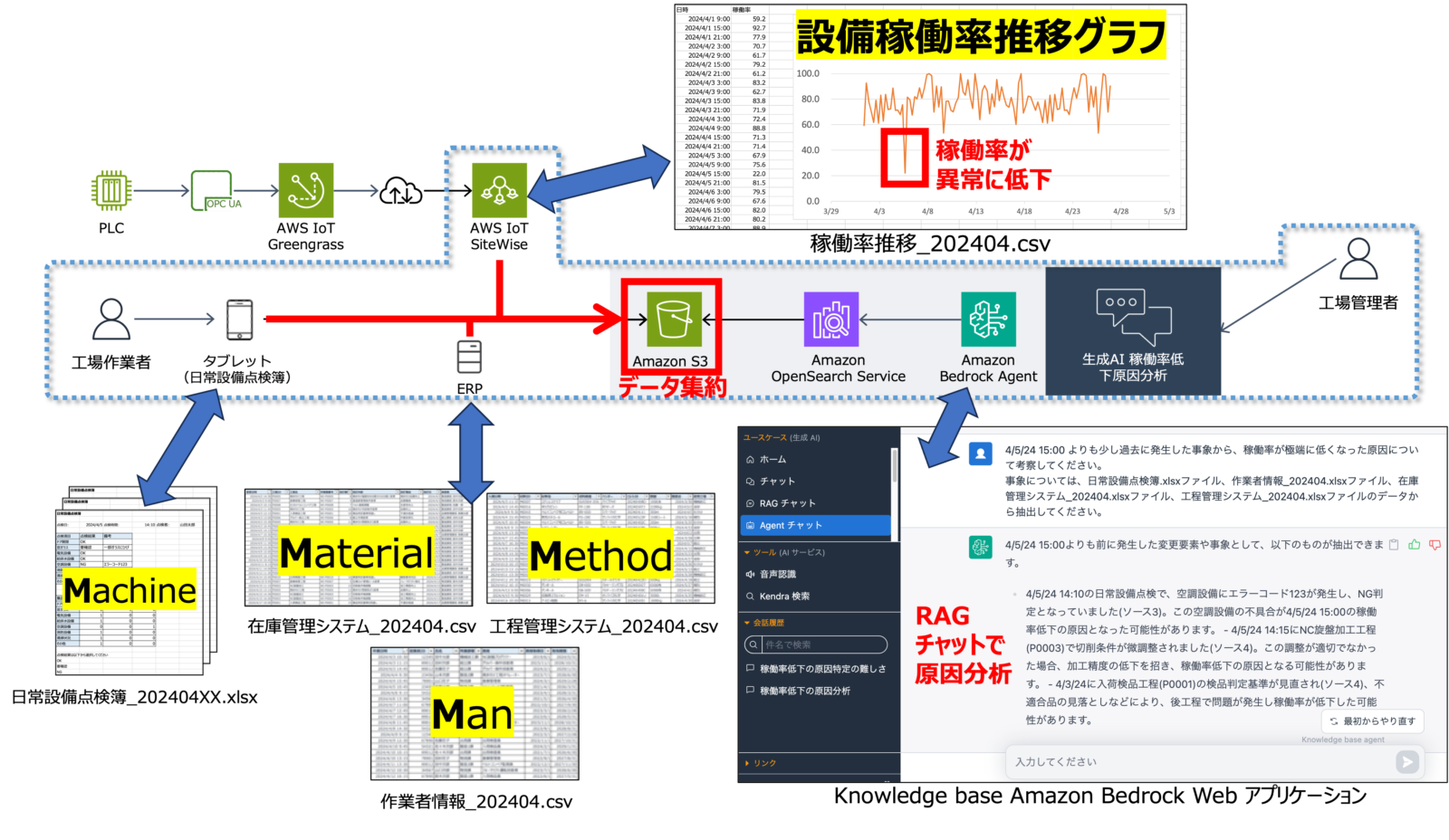
Amazonは、AWS Summit Japan 2024の展示で4M分析に生成AIを組み合わせ、稼働率低下の要因を4Mの視点から分析するユースケースを実施しました。
具体的には、ERPなど各種業務システムから抽出したデータを「Amazon S3」に集約し、RAGによって統合的に解析する仕組みです。
デモでは、稼働率が22.0%と急低下した日時を検出し、その直前の「日常点検簿」に記録された空調設備のエラーコード(123)を根本要因として特定するなど因果関係を正確に提示できました。
また、生成AIのRAG技術を使えば、社内データのPDFやWordなどのデータをもとに対話しながら分析できます。稼働率が閾値を下回った際に自動でアラートを出し、Amazon Bedrockに分析を依頼するパイプラインの構築により、自動分析も可能です。
スマートファクトリー実現のステップ
スマートファクトリー実現のためのステップを解説します。
ステップ1:データを収集・蓄積して可視化する
まず、IoT機器を活用してデータを収集・蓄積して情報を可視化します。製造工程での各機械のデータや製造に関するノウハウ、個人的な知見などを蓄積していきます。
例えば、設備にセンサーを取り付けてモニタリングすることで、設備の稼働状況を収集・監視できます。設備の稼働が多い時期や少ない時期、稼働が多い生産ラインなどの情報を得ることができるようになります。
このとき、収集・蓄積するデータは、すべての情報ではなく、目的を達成するために有益なデータかどうかを見極めることが大切です。
ステップ2:データ分析・予測
次に、収集・蓄積したデータを分析・学習し、目的達成に必要な要素の抽出や、モデル化、パターン化を行います。これにより、標準的な作業モデルの作成や過去データからの予測などを行うことができます。
例えば、収集した過去の稼働状況データを分析することで、今後の受注予測や設備の負荷が大きいものの整備時期などを予測することも可能になります。これらのデータは様々な種類で、かつ大量であるため、分析や予測にはAIを用いるのが有効です。
ステップ3:最適化
最後に、分析した将来の予測をもとに、生産計画や経営戦略の最適化を行っていきます。
例えば、今後の受注予測や設備の負荷の分析から、人員配置や資材調達、生産ラインの切り替えなど様々な戦略を立てていく必要があります。また、分析したデータから収益分析や設備の損耗度を把握し、適切な設備投資の計画・実行を行うこともできるようになります。
ここでは、IoTやAIの技術で得たデータをもとに人間が判断を下すことが重要です。データはあくまで判断を下す材料であり、最終判断を下すことは人間の仕事であることを意識しておく必要があります。
AI Marketでは、
貴社に最適な会社に手間なく数日で出会えます
スマートファクトリーを失敗しないためには
スマートファクトリー化で失敗しないためには、以下の点に注意する必要があります。
- 課題と目的を明らかにする
- マニュアル作成・研修を行う
それぞれの注意点を解説します。
課題と目的を明らかにする
スマートファクトリー化を失敗しないためには、現状の課題と目的を明らかにする必要があります。スマートファクトリー化というと、工場全てを機械化・自動化するために取り組む場合がありますが、まずは現状の課題・目的を明確化して必要な設備を洗い出すことが重要です。
スマートファクトリー化の失敗の原因の1つとして、コストによって最適化できないということが挙げられます。スマートファクトリー化のためのIoT機器やAI、システム構築など初期コストが膨大になり、予算不足で最適化することができないケースが多いのです。
目的に応じた設備やシステムを導入することで、予算内での最適化を行うことができるようになります。
マニュアル作成・研修を行う
スマートファクトリー化が形骸化してしまうのを防ぐためには、工場内の運用体制を事前に構築する必要があります。スマートファクトリー化を行うことで、これまでの生産フローや業務体制などが大きく変わります。いざ実運用を始めたときに、「現場からの問合せが相次ぐ」「現場が使いこなせない」といった問題が発生し、現場に定着せずに失敗に終わるケースもあります。
どのように業務が変わり、どのような効果が得られるのかを説明するとともに、業務内容・フローについては、マニュアルの作成や従業員への研修や教育を行うことで、スムーズに稼働することができ、定着しやすくなるでしょう。
スマートファクトリーについてよくある質問まとめ
- スマートファクトリー実現のステップは?
スマートファクトリー実現のステップは以下です。
- ステップ1:データを収集・蓄積して可視化する
- ステップ2:データ分析・予測
- ステップ3:最適化
- スマートファクトリーを失敗しないためには?
スマートファクトリー化で失敗しないためには、以下の点に注意する必要があります。
- 課題と目的を明らかにする
- マニュアル作成・研修を行う
まとめ
スマートファクトリーを成功させるためには、以下の手順で進めます。
- データを収集・蓄積して可視化する
- データ分析・予測
- 最適化
スマートファクトリー化を行う上で重要なのは、
しかし、スマートファクトリー化は初期コストが膨大になる可能性や、実運用で現場に定着せずに失敗するケースが多くあります。何でも自動化・機械化するのではなく、まずは
AI Marketでは、
貴社に最適な会社に手間なく数日で出会えます
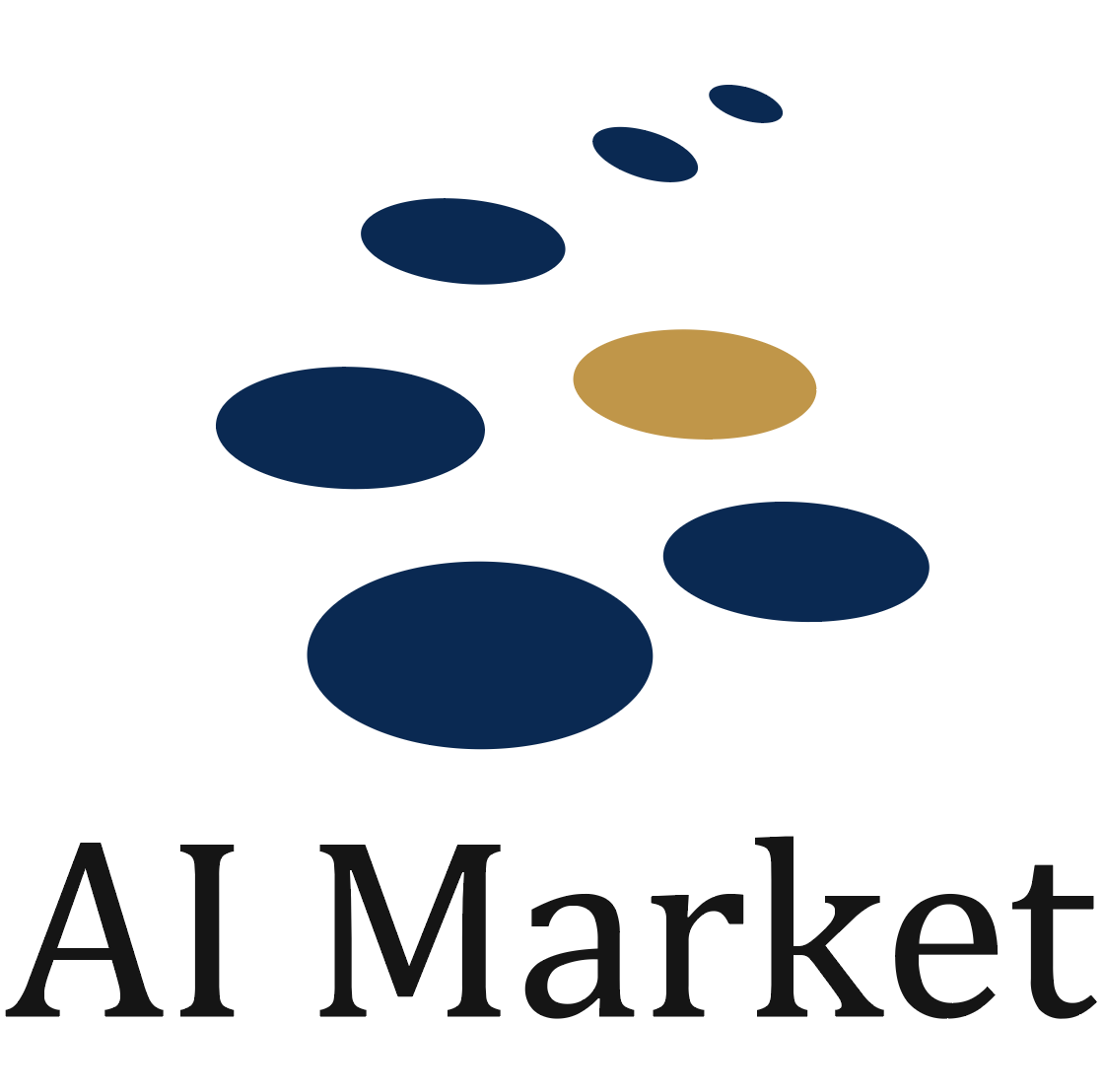
AI Marketの編集部です。AI Market編集部は、AI Marketへ寄せられた累計1,000件を超えるAI導入相談実績を活かし、AI(人工知能)、生成AIに関する技術や、製品・サービス、業界事例などの紹介記事を提供しています。AI開発、生成AI導入における会社選定にお困りの方は、ぜひご相談ください。ご相談はこちら
𝕏:@AIMarket_jp
Youtube:@aimarket_channel
TikTok:@aimarket_jp
運営会社:BizTech株式会社
弊社代表 森下𝕏:@ymorishita
掲載記事に関するご意見・ご相談はこちら:ai-market-contents@biz-t.jp
