溶接検査とは?抱える課題・外観検査AI活用のメリット・事例・導入手順を徹底解説!
最終更新日:2025年08月20日
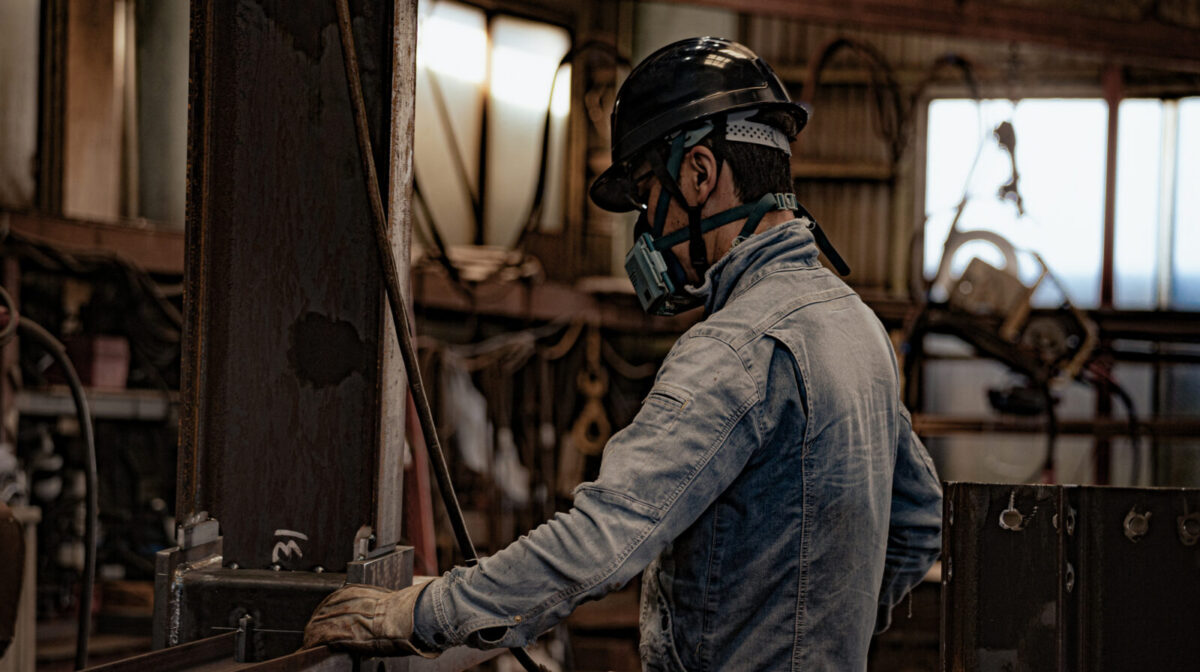
- 従来の溶接検査は、熟練者不足や人的要因によるばらつき、検出困難な欠陥といった課題を抱えており品質確保と効率化の両立が難しくなっている。
- AI技術(特に画像認識)を溶接検査に活用することで、検査精度の一貫性向上、検出漏れや過検出の削減、検査の高速化、属人化の解消といったメリットがある。
- AI導入を成功させるには、明確な目的設定、質の高い教師データの収集とアノテーション、段階的な現場実装と運用体制の構築が必要。
溶接工程は多くの製造業において基幹となる技術ですが、その品質を保証する溶接検査には、熟練者への依存、検査精度のばらつき、見逃しリスクといった根深い課題が存在します。
そこで近年、AI(人工知能)技術を活用した外観検査による溶接の検査が注目されています。
この記事では、溶接検査が直面する具体的な課題を整理し、AIがどのように課題を解決できるのか、そのメリット、活用される技術、実際の導入事例を交えて解説します。さらに、自社でAI導入を検討する際に不可欠となる実践的な手順も紹介しています。
外観検査に強いAI会社の選定・紹介を行います
今年度AI相談急増中!紹介実績1,000件超え!
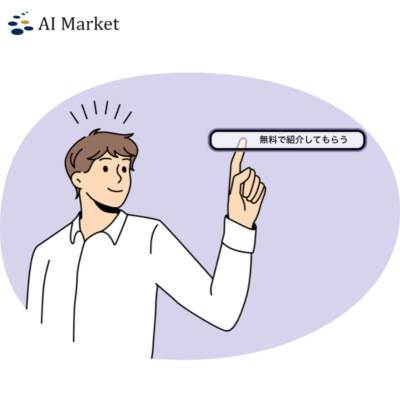
・ご相談からご紹介まで完全無料
・貴社に最適な会社に手間なく出会える
・AIのプロが貴社の代わりに数社選定
・お客様満足度96.8%超
完全無料・最短1日でご紹介 外観検査に強いAI会社選定を依頼する
製造業の外観検査に強いAI開発会社をご自分で選びたい場合はこちらで特集していますので併せてご覧ください。
溶接検査とは?
溶接検査は、溶接された部分(溶接部)が、設計図や仕様書、適用される規格(JIS, ASME, ISOなど)で要求される品質基準を満たしているかを確認するための重要な工程です。
検査により明らかになる欠陥には、以下のようなものがあります。
- 溶接ビードの不整合:形状や寸法のズレにより、設計基準から外れている部分を検出
- 内部欠陥:クラック、気孔、スラグの混入など、目視では確認が難しい内部の微細な不具合を検出
- 表面欠陥:亀裂や未溶着、表面の粗さなど、構造部材の耐久性に影響する欠陥を検出
溶接部の品質は、構造物やプラント、船舶、建築物などの安全性と耐久性の根幹をなしています。運用中の事故や故障を未然に防ぐためには、厳格かつ徹底した検査が不可欠です。
溶接検査は主に非破壊検査と破壊検査
溶接検査は、以下の「非破壊検査」と「破壊検査」の2種類に大きく分けられます。
非破壊検査は、製品を破壊することなく内部や表面の欠陥を検出する検査方法です。完成品に対しても実施できるのが特徴です。
非破壊検査の種類 | 特徴 |
---|---|
外観検査 |
|
液体浸透探傷検査 |
|
磁粉探傷検査 |
|
超音波検査 |
|
放射線検査 |
|
破壊検査は、溶接部を含む試験片を実際に破壊(切断、曲げ、引張りなど)して、その強度や性質を評価する検査方法です。主に溶接施工法の妥当性確認(WPS/PQR)、溶接技能者の技量確認、材料評価、研究開発などの目的で行われます。
破壊検査の種類 | 検査の特徴 |
---|---|
引張試験 | 材料に引っ張り力を加えることで、溶接部の引張強度と延性を評価する検査 |
曲げ試験 | 試験片に曲げ力を加え、溶接部の曲げ強度および靭性を評価する検査 |
衝撃試験 | 一定の条件下で急激な衝撃を与え、溶接部の靭性やエネルギー吸収能力を評価する検査 |
疲労試験 | 繰り返し荷重を加え、溶接部の繰り返し応力に対する耐久性や寿命を評価する検査 |
せん断試験 | 材料や溶接部にせん断力を加えせん断強度を評価する検査 |
圧縮試験 | 材料を圧縮することにより圧縮強度や耐圧性を評価する検査 |
トーション試験 | 材料にねじり力を加えて、溶接部のねじり強度やトーション耐性を評価する検査 |
対象となるワークの特性や要求に応じ、最適な検査手法を選定し、必要な検査を実施します。
溶接検査の手法
溶接検査の主な手法は、以下の3つです。
- 目視検査:熟練検査員が目で直接溶接部のビードやその他の形状・寸法の異常をチェック
- 自動検査:産業用カメラやセンサ、ロボットアームなどを組み合わせ自動的に検査
- AI検査:AIを活用することで、従来の目視や自動検査では見落としがちな微細な欠陥や複雑なパターンを高精度に検出
目視検査はさまざまな欠陥発見に有効です。しかし、検査員の技量、経験、集中力、体調に大きく依存するため、ばらつきが生じる点がデメリットです。
自動検査では、検査機器をロボットアームや自動走行装置などに取り付け、プログラムされた通りに自動で検査を実行します。溶接ビードの外観チェック、放射線検査など非破壊検査装置のデータを活用して内部欠陥を検出します。
検査速度の向上、検査品質の安定化(人的ミスの排除)、再現性の確保が期待できます。高温、狭隘、高所、放射線環境など、人による検査が困難な場所での検査も可能です。
AI検査では、自動検査などで取得した検査データ(画像、超音波信号など)を画像認識AIやデータ分析AIを用いて解析・判定します。表面の外観だけでなく内部構造の異常も網羅的に評価可能です。
従来の手法よりも検査プロセスの効率化が進み、品質管理のレベルが一層向上する点がメリットです。
外観検査に強いAI会社の選定・紹介を行います
今年度AI相談急増中!紹介実績1,000件超え!
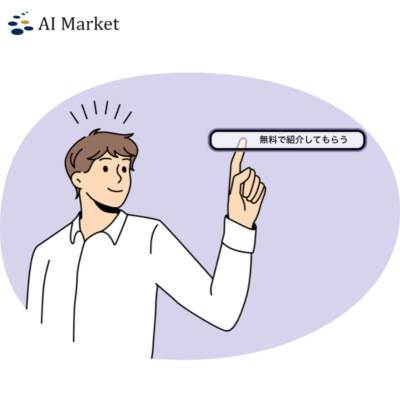
・ご相談からご紹介まで完全無料
・貴社に最適な会社に手間なく出会える
・AIのプロが貴社の代わりに数社選定
・お客様満足度96.8%超
完全無料・最短1日でご紹介 外観検査に強いAI会社選定を依頼する
現在の溶接検査が抱える課題
溶接検査では、複数の課題が現場で指摘されています。以下では、溶接検査が抱える課題を紹介します。
熟練労働者の不足
溶接検査において、正確な判断を下すためには豊富な経験と高度な技術力を有する熟練検査員が必要です。しかし、近年は技術継承の難しさや業界全体の高齢化、若手人材の確保難などの影響で、熟練労働者が不足しています。
熟練労働者の不足は、検査の信頼性に影響を及ぼし、品質確保や安全管理において重大なリスクとなっています。
人的要因への依存
現在、多くの検査現場では、比較的短い検査時間で全数検査を実施できる「検査員による目視検査」に大きく依存しています。目視検査は迅速かつ広範囲に対応できるメリットがある一方、微細な欠陥の見逃しや検査員ごとの主観的な判断により、検査結果にばらつきが生じるという課題があります。
また、長時間や単調な検査作業は、検査員の疲労や集中力低下を招き、微小な欠陥や予期せぬ欠陥の見落とし(ヒューマンエラー)につながるリスクがあります。目視検査への依存状態が、製品品質の均一性や信頼性に影響を及ぼすことが懸念されます。
検査員の負担増加
近年、溶接検査では検査員の負担増加が懸念されています。製品に対する安全性や信頼性の要求が高まり、より厳格な検査基準や規格への対応が求められています。
また、新しい材料(高張力鋼、アルミ合金、複合材など)や新しい溶接工法が登場し、それに適した検査技術や評価基準の確立が追いつかない場合があります。
特に自動車部品や大型構造物などでは、生産効率の向上や安全性要求の高まりに伴い、溶接部品自体が大型化・複雑化しています。その結果、一人当たりの検査対象が増加し、検査員にかかる負担が大幅に増加しています。
検査員の負担が大きくなると、過労や集中力の低下から検査精度が損なわれ、結果として検査ミスが発生しやすくなることから対策が急務です。
検出困難な欠陥の存在
非常に微細なき裂、特定の方向を向いたき裂、複雑な形状部の内部欠陥など使用する検査手法によっては検出が難しい、あるいは不可能な欠陥が存在します。
各検査手法には一長一短があり、万能な方法はありません。例えば、超音波探傷検査は表面近傍の欠陥検出を苦手とします。また、放射線検査は厚板や面の向きに垂直な割れの検出が苦手です。そのため、複数の手法を組み合わせる必要が生じ、コストや時間が増加します。
溶接検査でAIを活用するメリット
AIを溶接検査で活用するメリットは、従来の検査プロセスの課題を解消し、全体の検査精度と作業効率を大幅に向上させる点にあります。AIによる外観検査は、溶接検査だけでなく、はんだ付けや組立検査、半導体、ラベル、そしてガラス製品と言った製造業で不可欠な検査に活用されています。
以下では、AIを溶接検査で活用するメリットを紹介します。
過検出・検出漏れの削減
従来のパターンマッチングを用いた検査方法では、判定条件をあえて厳しく設定する傾向にあります。欠陥箇所のみを安定的に検出することが難しいので、不良製品の見逃しリスクを最小限にするためです。
その結果、本来合格品であっても検査装置が不良と判定してしまう「過検出」が発生しがちです。また、長時間の検査作業では検査員の疲労や集中力の低下が顕著となり、検品の歩留まりがさらに悪化します。
一方、AIは多種多様なパターンを学習し、微小な不良箇所を自動で抽出できます。浸透探傷・磁粉探傷では、現像された欠陥指示模様を画像として取り込み、AIが欠陥の種類や程度を自動で判定可能です。
そのため、検出漏れを大幅に減少させる効果が期待できます。製品の品質向上が実現され、より信頼性の高い検査結果を得られるでしょう。
高精度な検査
AIは学習したデータに基づいて客観的かつ一貫した基準で判定を行うため、人間の検査員による主観や経験、疲労による判定のばらつきを低減できます。X線写真(フィルムまたはデジタル画像)から、ブローホール、スラグ巻込み、融合不良、割れなどの内部欠陥を自動で検出・分類・計測することが可能です。
微細な欠陥や、人間が見逃しやすい複雑なパターンの欠陥も、AIは安定して検出できる可能性があります。
検査の高速化
AIは大量の検査データ(画像や信号)を人間よりもはるかに高速に処理・解析できます。AIを活用することで、リアルタイムで膨大なデータの解析が可能です。
これにより、検査時間を大幅に短縮し、生産ラインのボトルネック解消やリードタイム短縮に貢献します。
人手不足の解消
溶接検査では目視検査に依存しており、熟練検査員と未熟な検査員の間で製品検査の精度に大きな差が生じるケースが散見されます。特に、人が一つひとつ溶接打点を確認する目視検査では、膨大な作業工数が発生し、重要な箇所が見落とされるリスクも高まります。
AIを導入することで、検査プロセス全体を標準化し、どの担当者が実施しても一貫した精度で検査を行える環境を実現できます。属人的な技量の差に起因する品質ばらつきを解消し、全体の生産効率と信頼性の向上が可能です。
暗黙知となりがちな熟練者の技術をAIという形で形式知化し、技術継承の一助とすることも期待されます。
データ活用の促進と予知保全への応用
検査データをAIで解析し、欠陥の傾向や発生原因を特定することで、溶接プロセス自体の改善(パラメータ最適化など)に繋げられます。蓄積されたデータから、将来的な欠陥発生や設備の異常を予知する「予知保全」への応用も期待されています。
外観検査に強いAI会社の選定・紹介を行います
今年度AI相談急増中!紹介実績1,000件超え!
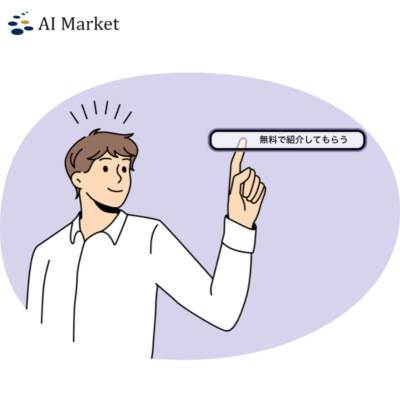
・ご相談からご紹介まで完全無料
・貴社に最適な会社に手間なく出会える
・AIのプロが貴社の代わりに数社選定
・お客様満足度96.8%超
完全無料・最短1日でご紹介 外観検査に強いAI会社選定を依頼する
溶接検査でAIを活用している事例
実際にAIを活用し、溶接検査においてコスト削減や誤判定率の削減に成功している企業もあります。
AI検査で幅広い溶接欠陥を検出(パナソニックコネクト)
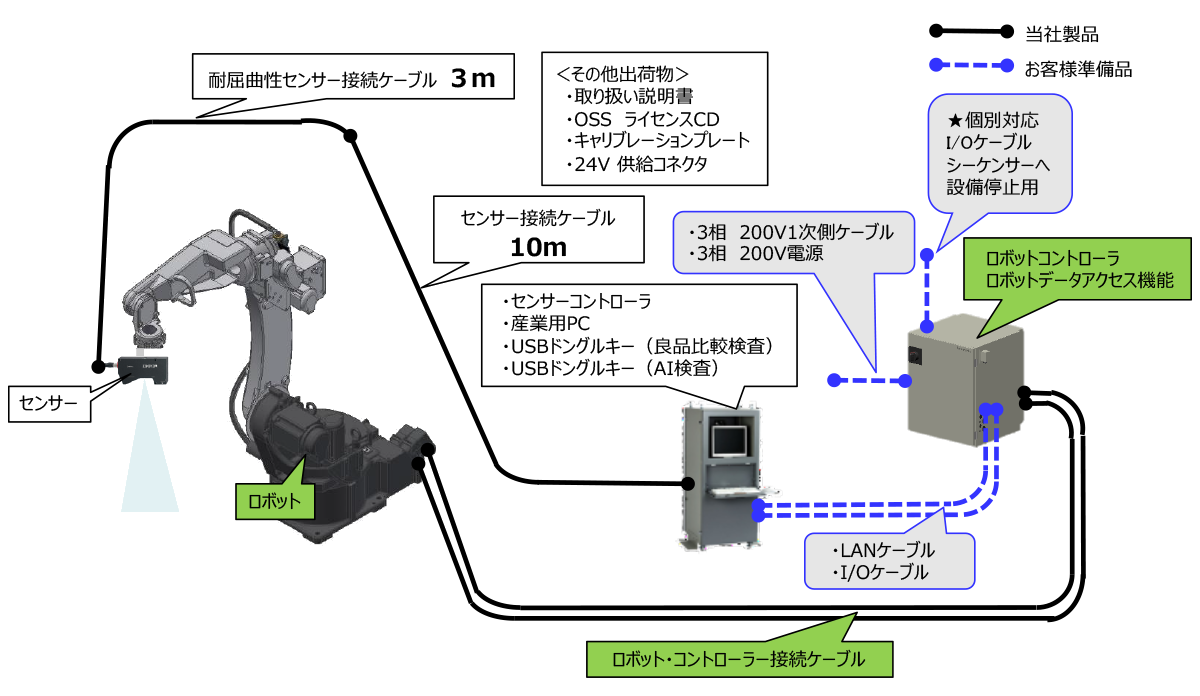
パナソニック コネクト株式会社は、溶接検査の精度向上と検出漏れの低減を目指し、以下のように良品比較検査とAI検査を融合した高度な検査システム「Bead Eye」を開発しました。
- 良品比較検査で判定:事前に設定した良品データと形状を比較、一致率をもとに良否判定
- AI検査で判定:パナソニックで学習済みのAIエンジンにより、欠陥の形状を学習し、欠陥の種類と位置を判断し、微小な欠陥も簡単に検査
また、本システムで登録される良品マスタには以下の多項目が含まれており、これらの項目との比較によって溶接部の状態を評価します。
- ビード欠け
- ビード位置ズレ
- 余盛不足/過多
- ビード幅不足/超過
- ビード長さ不足/超過
- 穴あき
- ピット
- アンダーカット
- スパッタ
本システムは、これまで自動外観検査が苦手としていた微細な溶接欠陥もロボットによる一貫した検出を可能としています。
溶接部のビードの外観検査自動化(岡部機械工業)
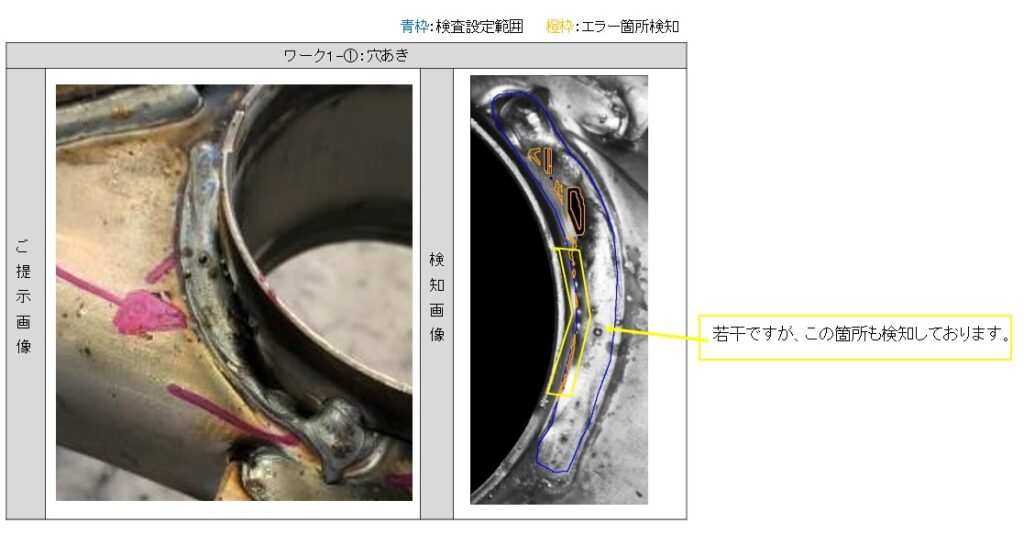
株式会社岡部機械工業は、LMI社製Gocator3200シリーズを搭載した縞投影式3次元画像センサと、6軸ロボットを組み合わせ、溶接部のビードにおける外観検査の自動化を実現しています。
本外観検査システムの特徴は、センサにより取得された画像を画像処理ソフトウェア「HALCON」にて取り込み、高さ情報を加味している点です。
HALCONには豊富なフィルタ処理や欠陥検査機能が搭載されており、ルールベースの画像処理アルゴリズムでは検出できない欠陥でも複雑な特徴量解析を組まずに検出できるソフトウェアです。画像処理関数群の中の1つとして、簡単に自社アプリケーションの中にディープラーニング機能を組み込めるようになっています。
例えば、穴が空いている箇所は、正常部分と比較して高さ情報が大きく低下し、黒く欠落した領域として認識されます。検査ソフトでは、上記のように穴あきを橙色枠でハイライトし、エラー箇所として分かりやすく表示可能です。
このように、本システムは形状が複雑かつ凹凸のある対象の外観異常に対して、3次元スキャナと画像処理ライブラリHALCONを組み合わせることで高精度な検査を可能としています。
スポット溶接打点の検査の手軽さ・正確性を向上(アルモニコス)
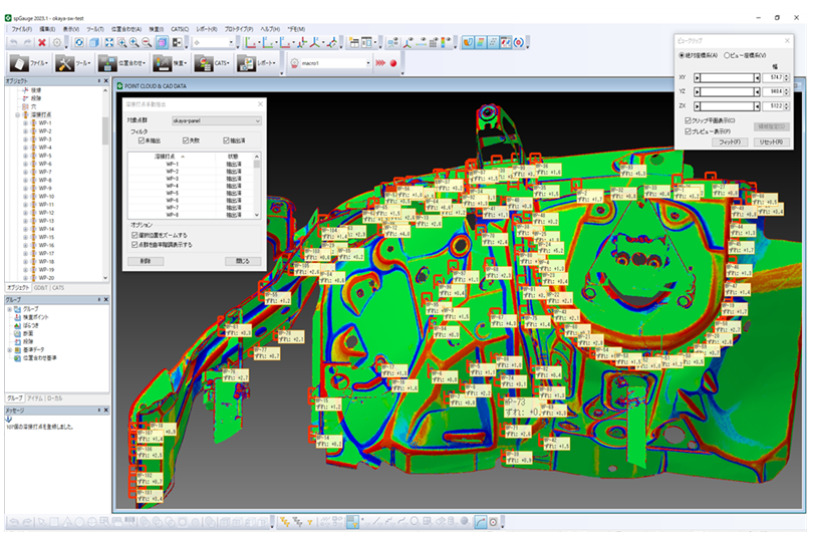
株式会社アルモニコスは、3Dスキャナで測定した点群データと設計データを活用する検査ソフト「spGauge」を提供しています。
従来、打痕の有無や位置の確認には目視検査や有接触測定などの手法が用いられていましたが、正確性と効率性の点で課題がありました。
例えば、従来の目視確認では、打痕の有無は確認できるものの、位置の正確さや微妙なズレの測定は困難でした。また、有接触測定機による検査では座標位置の確認は可能ですが、手作業のため手間や時間がかかり全体工程の効率化が難しいという課題がありました。
このような従来法の課題を解決するために、spGaugeは打痕に投影した曲率階調色の画像をAIに判別させることで溶接打点位置の検査を可能としています。この方法により、テスト結果の中には、従来の検査機能で20カ所発生した誤検出が1カ所にまで削減できたケースもあります。
非接触測定データとAIを活用した検査方法により、現物の測定から検査、レポート作成まで、従来法に比べ大幅に測定の手間や時間を削減できるだけでなく、手軽に高精度な溶接打点検査を実現します。
AI溶接検査の導入手順
溶接検査にAIを導入する手順は、以下のとおりです。
- 目的設定と課題特定
- 検査手法とデータ取得環境の定義
- 溶接欠陥データの収集とアノテーション
- AIモデル構築と溶接基準に基づく性能検証
- 実ラインへの実装と継続的モニタリング
- 運用体制の構築と教育
1.目的設定と課題特定
- どの製品・部品の、どの溶接方法(アーク、レーザー、抵抗など)、どの箇所(材質、板厚、継手形状)の検査にAIを適用するか具体的に定義
- 現行の検査方法における具体的な課題を特定・定量化
例: 特定欠陥の見逃し率、検査員のスキル依存、検査時間、コスト - 対象溶接部に適用される品質規格(JIS, AWS, ISOなど)と合否判定基準を確認
- AI導入によって何を達成したいかを具体的かつ測定可能な目標として設定
例: 検査時間〇〇%削減、特定欠陥検出率〇〇%向上、判定基準の客観化 - 溶接技術者、品質管理担当、NDT検査員、生産技術者など関係部署と初期段階から連携し、目的と実現可能性を共有
- 導入・運用コストと、期待される効果(品質向上、コスト削減、生産性向上)を考慮した費用対効果を試算
関連記事:「 AI開発・生成AIシステム開発・導入の費用相場は?」
2.検査手法とデータ取得環境の定義
- AIが解析する元データを選択
例: 外観検査用高解像度カメラ画像、デジタルX線画像(DR)、自動UTのスキャンデータ(B/C/Dスコープ)、PT/MTの欠陥指示模様画像など - 欠陥を安定して捉えるための条件を決定
例: カメラの解像度・画角、照明の種類・角度・強度、UT探触子の種類・周波数・スキャンピッチ、RTの撮影条件 - 検査対象の搬送、センサーの位置決めなどを自動化(ロボット等)するか検討
- 安定したデータ取得のため、外乱光、振動、温度変化などの影響を最小限にする環境を整備
- AIモデルの学習・推論を行うソフトウェア、データ管理基盤、既存システム(MES, QMS等)との連携方式を選定
関連記事:「AIの開発環境に必要なのは?必須のハードウェア・ソフトウェア」
3.溶接欠陥データの収集とアノテーション
- 良品データに加え、対象となる全種類の溶接欠陥を網羅的かつ多様なパターン(サイズ、位置、形状)でデータを収集
意図的に欠陥試験片を作成することも検討 - 実際の生産ラインやそれに近い環境で、様々な変動要因(表面状態、位置ずれ等)を含んだデータを収集
- 収集したデータに対し、有資格の溶接検査員やNDT技術者が適用規格に基づき欠陥の種類、位置、サイズ、合否判定などの正確なラベルを付与(アノテーション)
単なる「OK/NG」だけでなく、欠陥の種類や等級(例: JIS Z 3104の等級分類)までラベリング
4. AIモデル構築と溶接基準に基づく性能検証
- データ特性とタスクに適したAIモデル(例: CNN、物体検出モデル)を選定し、アノテーション済みデータで学習させる
- 溶接検査の目的に合った評価指標を設定
例: 欠陥検出率、非欠陥誤検出率、欠陥種別ごとの正解率、欠陥寸法の誤差 - 未学習のデータセットを用いて性能を評価
可能であれば、熟練検査員の判定結果とAIの判定結果を比較検証(ブラインドテスト等) - AIの判定結果が、適用される溶接規格の合否判定基準を満たせるか検証
- 評価結果に基づき、データ追加(特に判定が難しかったケース)、パラメータ調整、モデル構造変更などの改善サイクルを回す
5. 実ラインへの実装と継続的モニタリング
- 可能であれば、オフラインでの試行や一部ラインでの先行導入から始め、問題点を洗い出して修正
- 検査装置、生産ライン制御システム(PLC)、製造実行システム(MES)、品質管理システム(QMS)などと連携し、検査結果の自動記録やトレーサビリティを確保
- AIが欠陥と判定した場合の処置(など、AI導入後の検査・品質保証プロセスを明確に定義
例: 自動排除、アラート、人間による再確認 - AIの判定精度、処理速度、誤検出率などを継続的に監視し、性能劣化(モデルドリフト)がないか確認
- 製造プロセスや材料、製品仕様の変更、新たな欠陥傾向の出現などに対応するため定期的なメンテナンスやAIモデルの再学習・更新計画を策定
6. 運用体制の構築と教育
- AIシステムの操作担当者、監視担当者、メンテナンス担当者、データ管理・再学習担当者などの役割と責任を明確にする
- AI検査システムの操作方法、判定結果の見方(信頼度スコア等)、AIが苦手とするケース、異常時の対応、手動確認手順などを現場の検査員や作業者に教育・訓練
- AIを用いた検査プロセスのための標準作業手順書を作成し、周知徹底する
- 現場からの問い合わせ対応、トラブルシューティング、改善提案を吸い上げる体制を構築
外観検査に強いAI会社の選定・紹介を行います
今年度AI相談急増中!紹介実績1,000件超え!
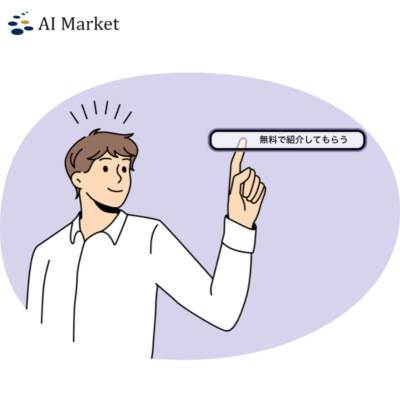
・ご相談からご紹介まで完全無料
・貴社に最適な会社に手間なく出会える
・AIのプロが貴社の代わりに数社選定
・お客様満足度96.8%超
完全無料・最短1日でご紹介 外観検査に強いAI会社選定を依頼する
溶接検査についてよくある質問まとめ
- 超音波やX線などの非破壊検査データもAIで解析できますか?
はい、AIは非破壊検査データもリアルタイムで解析可能です。超音波やX線データを高速に処理することで、内部欠陥や密度の異常などを正確に検出し、検査精度の向上につながります。
- 溶接検査にAIを導入すると、具体的にどのようなメリットがありますか?
AI導入により、以下のメリットが期待できます。
- 熟練度に関わらず一貫した高精度な検査が可能になり、見逃しや過検出が削減される
- 検査時間が短縮され生産性が向上する
- 検査結果がデータとして蓄積され、プロセス改善や予知保全に活用できる
- 属人化を解消し技術継承にも貢献する
まとめ
溶接検査は、構造物や建築物などの安全性・耐久性に直結する重要な工程です。従来の目視検査では検査精度のばらつきや作業負荷の増大が問題視されており、近年はAIを活用した外観検査技術が注目されています。
しかし、AI導入を成功させるためには、自社の溶接プロセスや対象製品、適用される規格を深く理解した上で、適切なデータ戦略、モデル選定、そして厳密な性能検証が不可欠です。特に、品質保証に関わる重要なプロセスであるため、その導入と運用には慎重な計画と専門的な知見が求められます。
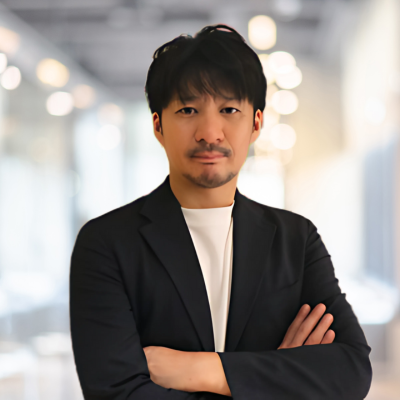
AI Market 運営、BizTech株式会社 代表取締役|2021年にサービス提供を開始したAI Marketのコンサルタントとしても、お客様に寄り添いながら、お客様の課題ヒアリングや企業のご紹介を実施しています。これまでにLLM・RAGを始め、画像認識、データ分析等、1,000件を超える様々なAI導入相談に対応。AI Marketの記事では、AIに関する情報をわかりやすくお伝えしています。
AI Market 公式𝕏:@AIMarket_jp
Youtubeチャンネル:@aimarket_channel
TikTok:@aimarket_jp
運営会社:BizTech株式会社
掲載記事に関するご意見・ご相談はこちら:ai-market-contents@biz-t.jp
