ガラス外観検査とは?現状の課題・AIを活用した自動検査のメリット・事例・導入方法を徹底解説!
最終更新日:2025年04月27日
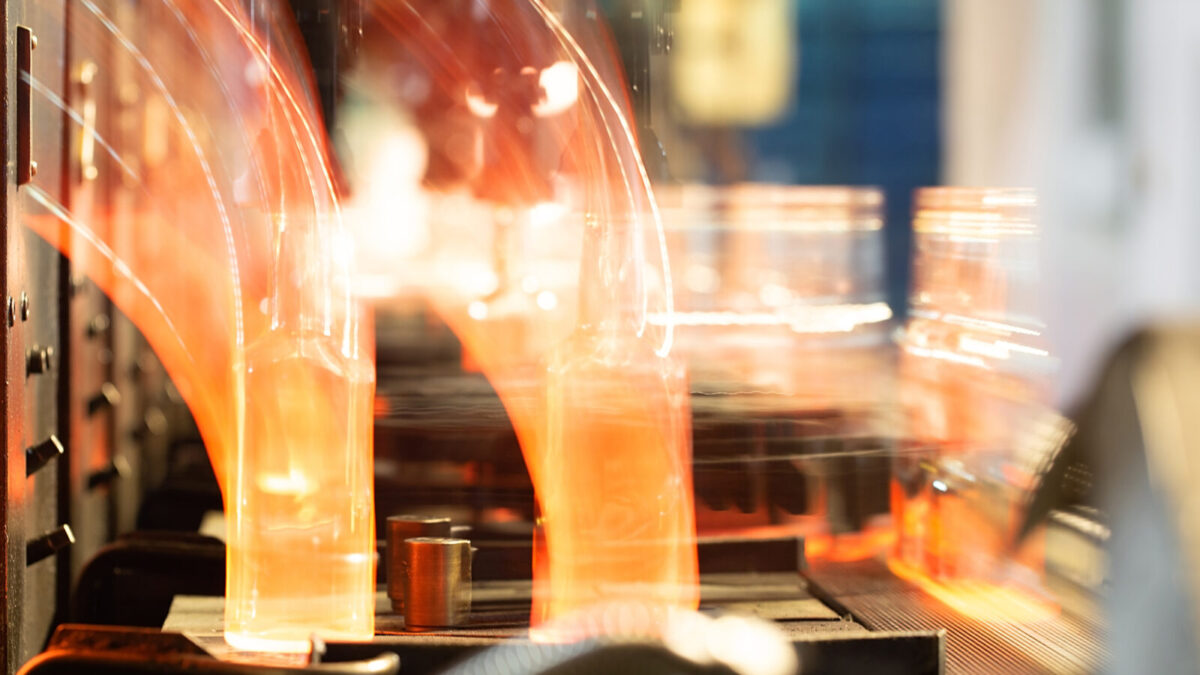
- 従来のガラス外観検査(目視やルールベース)では、微小欠陥の見逃しや判定のばらつき、熟練者不足といった課題
- AI(特にディープラーニング)を活用することで、これらの課題を克服し、検査精度、速度、安定性を大幅に向上
- AI導入を成功させるには、現状課題の明確化、適切な撮像環境の構築、質の高いデータ準備、段階的な導入と評価といった実践的なステップが不可欠
ガラス製品の品質を左右する外観検査は、ガラス製品の表面に潜む微細な欠陥や不良部位を検出し、電子機器などの安全性を保証するための重要な工程です。熟練オペレーターによる目視検査に依存している傾向にあり、見逃しや検査結果のばらつきといった課題が指摘されています。
本記事では、こうしたガラス外観検査特有の課題に対し、AI、特にディープラーニングを活用することで、いかに精度と効率を飛躍的に向上させられるかを解説します。AI導入による具体的なメリットから、成功に不可欠な実践的導入ステップ、実際の活用事例までを網羅しています。
自社の検査プロセスを改善し、品質と生産性を両立させるための具体的な道筋が見えてくるはずです。
AI Marketで
製造業の外観検査に強いAI開発会社をご自分で選びたい場合はこちらで特集していますので併せてご覧ください。
目次
ガラス外観検査とは?
ガラス外観検査とは、ガラス製品(板ガラス、レンズ、容器、部品など)の表面に存在するさまざまな欠陥や不良を迅速かつ正確に検出する検査です。場合によっては内部に見える欠陥や不具合もチェックします。
ガラスは、建築物や自動車、電子機器、医療機器、食品容器などの幅広い分野で利用され、ほんの僅かな欠陥でも製品全体の性能や外観、使用中の安全性に影響を与える恐れがあります。特に近年は、製品の高機能化・小型化に伴い、より微細な欠陥の検出が求められるようになっています。
したがって、ガラス外観検査は、最終製品が厳格な品質基準を満たし、製品の安全性や信頼性を保証するために重要な工程といえます。
ガラス外観検査の対象となる主な欠陥
具体的には、以下のような欠陥を検出します。
- キズ(線状、点状)
- 打痕、欠け(カケ)、ヒビ(クラック)
- 汚れ、付着物、シミ
- 気泡(表面にあるもの、または表面から見えるもの)
- 異物(表面に付着または内部から見えるもの)
- コーティングムラ、ピンホール
- 歪み(ひずみ)、うねり
- 指紋、油膜
上記に挙げたような表面上の欠陥に加えて、規定外の厚み、反りやエッジ部分の形状不良と言った、形状・寸法の異常も検査対象となることがあります。
ガラス外観検査の主な手法
ガラス外観検査は主に非破壊検査が用いられます。その際の手法は主に以下の3種類です。
- 目視検査:熟練のオペレーターが直接ガラス表面を観察し、傷や気泡、変色などの不具合を判断する
- 自動化検査システム:画像処理技術を利用したシステムにより、高速かつ高精度に検査を行う
- AIを活用した外観検査システム:大量の検査画像から微細なガラス不良を自動的に検出・分類する
目視検査は、オペレーターの豊富な経験とノウハウを活かして、微細な異常を柔軟に検出できる点が大きな強みです。その一方、オペレーターごとの主観や疲労、照明などの環境条件に影響されやすい課題があります。
また、自動化検査システムは検査結果の再現性が向上し、人的ミスが大幅に低減されるため、生産ラインの効率アップに貢献します。一方、照明やガラスの種類に依存し、環境調整や工夫を要する点がデメリットです。
画像認識AIによる自動外観検査システムは、従来見逃しがちだった欠陥の検出が可能となり、不良品の混入防止につながるため、目視検査や従来のルールベースによる自動検査システムに代わる手法として注目されています。
▼累計1,000件以上の相談実績!お客様満足度96.8%!▼
ガラス外観検査が抱える課題
ガラス外観検査では、以下に挙げるさまざまな課題を抱えています。
- 検出漏れ・過検出
- 熟練オペレーターの不足
- 微小欠陥・低コントラスト欠陥の検出限界
- 複雑形状・多様な材質への対応
ガラス外観検査における課題を説明します。
検出漏れ・過検出
目視検査に依存する場合、オペレーターの判断ミスや見落としが発生しやすく、実際に存在する微細な傷やクラックが検出されないことも少なくありません。検査員の熟練度、集中力、疲労度によって判定結果がばらつく「人的要因」は依然として大きな課題です。
また、カメラや各種センサなど専用の機械を用いた検査でも、ガラス表面に付着したホコリ、洗浄ムラ、あるいは素材自体の許容範囲内のばらつきなどが欠陥として誤認識される「疑似欠陥」の問題があります。
そのため、従来の手法によるガラス外観検査では、欠陥検出漏れのリスクを抱えています。
熟練オペレーターの不足
ガラス外観検査では、光学的な検査でも見つけるのが困難な微細なクラックなどの欠陥を検出する必要があります。そのため、目視検査では長年の経験と高度な判断応力を持つ熟練したオペレーターが不可欠です。
しかし、近年は熟練オペレーターの退職が増え、検査のニーズに対して熟練した技術を持つ人材が不足している状態です。少子高齢化や技術継承の問題から、経験豊富な熟練検査員が不足しており、育成にも時間とコストがかかります。
熟練オペレーターの経験だけに依存することが限界となり、自動検査システムによる代替が必要に迫られている現場もあります。
微小欠陥・低コントラスト欠陥の検出限界
近年、ガラスを用いる製品の大面積化かつ薄型化が進む中で、要求される欠陥の大きさが目視検査の限界を超えつつあります。スマートフォン、センサー、精密光学部品など、製品の高機能化・小型化に伴い、検出対象となる欠陥サイズもμm(マイクロメートル)オーダーと非常に小さくなっています。
例えば、ディスプレイや半導体基板では、広大な面積にわたって非常に微細なクラックが発生する可能性があり、微細な欠陥を従来の目視検査で迅速かつ正確に検出するのは、熟練オペレーターであっても困難です。
ガラス表面の薄いコーティングムラ、ごくわずかな歪み、内部の微細な脈理(屈折率の不均一)などは、健常部との輝度差(コントラスト)が小さく、判別が非常に困難です。
このような目視検査の限界は、従来の手法だけでは対処しきれない検査精度やスピードが要求される現代の製造現場において、検査工程改善の必要性を強く示しています。
複雑形状・多様な材質への対応
自動車のフロントガラス、レンズ、デザイン性の高い容器など、平面でないガラス製品が増えています。曲面や凹凸があると、均一な照明を当てることが難しく、カメラの焦点も合いにくいため、検査精度が低下したり、検査範囲が限定されたりする課題があります。
材質についても、強化ガラス、合わせガラス、コーティングガラス、特殊な添加剤を含むガラスなど種類や特性が多様化しています。それぞれ光学的特性(透過率、反射率など)が異なるため、材質ごとに最適な検査条件(照明、カメラ設定、アルゴリズム)を見つける必要があります。
▼累計1,000件以上の相談実績!お客様満足度96.8%!▼
AIをガラス外観検査で活用するメリット
AIをガラス外観検査に取り入れることで、検査品質などでメリットをもたらします。AIによる外観検査は、ガラスだけでなく、組立検査や溶接検査、はんだ付け、ラベル外観検査、そして半導体と言った製造業で不可欠な検査に活用されています。
ここでは、AIをガラス外観検査で活用する以下のメリットを紹介します。
- 欠陥の高精度検出
- 外観検査スピードの向上
- オペレーターの負担軽減
- データ活用による工程改善
欠陥の高精度検出
高精度なAI外観検査システムでは、微細な傷やヒビ、気泡などの欠陥を自動的に検出し、欠陥の種類ごとに正確な分類が可能です。
ディープラーニング、特にCNN(畳み込みニューラルネットワーク)を用いた高度な画像認識AIは、画像の中から自動的にキズ、気泡、汚れ、異物、コーティングムラなど、多種多様な欠陥の種類を高精度に識別します。
また、セグメンテーションを使えば欠陥領域をピクセル単位で精密に特定しますので、欠陥の正確なサイズや形状測定に繋がります。
例えば、従来の目視検査では保護フィルムの汚れをガラス状の欠陥と誤認識するケースが多々ありましたが、AIの外観検査システムは欠陥と汚れの違いを的確に判定できるため、検出精度が大幅に向上します。
不良品の混入を効果的に減らし、製品の品質保証に貢献します。
関連記事:「製造業での画像認識AI導入事例は?効果や活用事例を徹底解説!」
外観検査スピードの向上
AI外観検査システムはリアルタイムで検査画像を解析できる機能があるため、検査ライン全体のスピードが向上します。一度学習モデルが構築されれば、高速な画像処理が可能となり、生産ラインのスピードに対応したインラインでの全数検査を実現しやすくなります。
結果として、生産効率が向上し、製造工程におけるコスト削減や短納期対応が可能になるなど、全体のオペレーション改善につながります。
オペレーターの負担軽減
ガラスの外観検査では、ガラス特有の反射や屈折により、撮影時に光が跳ね返るため正確な画像取得が難しく、照明条件の微妙な違いが検査結果に大きな影響を与えることも多くあります。そのため、検査現場ではオペレーターに煩雑な作業や高い集中力が求められ、過度な負担がかかりがちです。
これらの煩雑で集中力のかかる検査作業をAIに任せることで、オペレーターの負担軽減とともに、高度な判断や設備管理など付加価値の高い業務に専念できるようになります。
目視検査への依存度を減らし、検査工程の自動化を促進することで、人件費の削減や、熟練検査員の不足といった課題の解消に貢献します。
データ活用による工程改善
検出された欠陥の種類、位置、サイズなどのデータを蓄積して分析することで、不良発生の原因究明や製造プロセスの改善に繋げることが容易になります。
AIによるガラス外観検査事例
実際にAIを活用し、ガラス外観検査においてコスト削減や誤判定率の削減に成功している企業もあります。以下では、AIを活用したガラス検査の事例を紹介します。
曲面・ガラス面向けの外観検査ロボットを提供(AIハヤブサ)
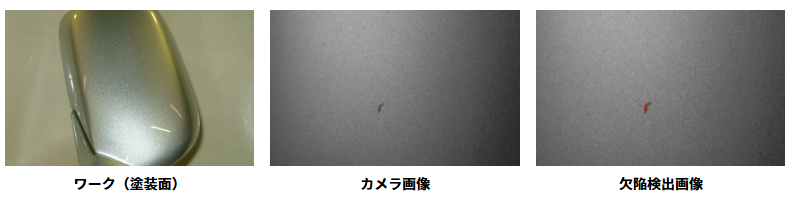
株式会社AIハヤブサは、曲面や鏡面など、平坦ではない複雑な表面に対応できる外観検査ロボットを開発しました。
具体的には、多関節ロボットがワークの曲面に合わせてカメラヘッドを最適な位置に配置し、専用の光学系により微細な欠陥を的確に捉えます。取得した画像から擦り傷やピンホール・打痕・ブツ・へこみの他、塗装やメッキの色ムラなどを抽出・画像解析します。
導入により、肉眼では見逃しがちな不良を確実に発見することが可能となり、検査精度の向上が期待できます。
ガラス製品のAI欠陥検査で99.8%の判別精度を実現(東京エレクトロン デバイス)
東京エレクトロン デバイス株式会社が支援する、あるディスプレイパネルの製造プロセスでは、ガラス表面の傷検査や液晶の偏光板フィルムの不良検査など、さまざまな検査が行われます。
検査対象の製品は、出荷時にガラス面に傷がつかないように保護フィルムで覆われていますが、従来のルールベースによる画像処理だけでは、外部の保護フィルムの汚れと内部の偏光板フィルムの欠陥を正確に区別することが困難でした。
そこで、約5,000枚〜10,000枚にのぼる膨大な画像データをAIに学習させることで、精度の向上を図りました。導入の結果、検査システムは99.8%の高い正解率で欠陥を判別できるようになり、従来の人的検査に比べて大幅なコスト削減と効率化を実現しています。
IoT対応AI外観検査システムで誤判定を1%未満まで抑制(AFC)
株式会社AFC研究所が支援を行っているある製造現場では、毎分数十本のペースで生産しているガラス瓶の口元の欠けを検査する工程において、目視検査の効率化を検討していました。
1日に数万本のガラス瓶を正確に目視で検査し続けるのは、オペレーターの集中力に限界があり、不良品が後工程へ流出していたためです。
そのような背景のもと、生産ラインのベルトコンベア上で透明ガラス瓶を横方向から複数カメラで検査するシステムを検討していた。しかし、透明ガラス瓶特有の光透過や高光沢による後面の映り込み、反射などの問題から、従来の外観検査装置では対応できるものがありませんでした。
従来型の検査システムに代わり、複数社のAI外観検査システムを検証した結果、従来のシステムは検出精度が低い上に、AIの学習モデルの構築に半日から1日程度かかるため、チューニングに非常に時間がかかり、希望する検出精度を達成できないという課題に直面していました。
そこで、AFCのIoT対応AI外観検査システム「FALCON」でワークテストデモを実施した結果、わずか15分程度でモデル構築が完了し、短時間ながらも異常部を的確に検出できることが確認でき、本格検討を決定しました。
初期段階では透明ガラス特有の透過や反射により正常品を誤検出するケースがあったところ、撮像環境の最適化と検査条件の綿密な調整により、誤判定率を1%未満にまで抑制することに成功しました。
AIガラス外観検査の導入手順
ガラス外観検査にAIを導入する手順は、以下のとおりです。
- 現状把握と導入目的の明確化
- 検査仕様の定義と最適な撮像環境の構築
- 高品質な教師データの収集とアノテーション
- AIモデルの学習と精度検証
- 生産ラインへの実装と実運用評価
- 運用体制の構築と継続的な改善
現状把握と導入目的の明確化
まず、AI導入の目的を具体的に定義することから始めます。
現在、どのような種類のガラス製品を対象に、どのような方法で検査しているか、その精度、速度、コスト、人員体制を詳細に把握します。次に、現状の検査で見逃しやすい欠陥や、自動化したい工程、判定のばらつきなど、具体的な課題をリストアップします。
そして、特定した課題に基づき、以下のような定量的で達成可能な目標を設定します。
- 「〇〇(欠陥名)の検出率を〇%向上させる」
- 「検査タクトタイムを〇秒短縮する」
- 「目視検査員〇名分の工数を削減する」
必要であれば、限定的な範囲でPoC(概念実証)を行い、技術的な実現可能性や期待される効果を事前に検証します。予算、スケジュール、必要な人材(AIエンジニア、品質管理担当、現場オペレーター)についても計画を立てます。
検査仕様の定義と最適な撮像環境の構築
AIの性能は「どのような画像を入力するか」に大きく左右されます。ガラス特有の性質を考慮した撮像環境の構築が極めて重要です。
AIで検出したい欠陥の種類とその許容基準を明確に定義します。良品と不良品の境界線を具体的に定めます。
最適な撮像手法の選定も必要です。
- 照明:ガラスの透明性、反射性を考慮し、欠陥の種類に応じて最適な照明を選定・組み合わせます。外乱光の影響を最小限に抑える工夫も必要です。
例:同軸落射、透過照明、暗視野照明、偏光照明、マルチアングル照明など - カメラ・レンズ:検出したい欠陥のサイズや検査範囲、ガラスの厚み・曲率に応じて、適切な解像度を持つカメラと、歪みが少なく焦点深度の合うレンズを選定します。
- 撮像タイミング・位置:ガラス製品の搬送方法(コンベア、ロボットハンドなど)に合わせて、振動の影響を受けず、安定した位置で、かつ必要な箇所を確実に撮像できるタイミングと位置を設定します。
- ハードウェア・ソフトウェア選定:上記仕様を満たすカメラ、レンズ、照明、PC、そしてAI推論を実行するためのソフトウェア(AIプラットフォームやライブラリ)を選定します。将来的な拡張性やメンテナンス性も考慮します。
高品質な教師データの収集とアノテーション
AIモデルの「教師」となる画像データの質と量が、検査精度を決定づけます。実際の生産ラインに近い環境で、定義した撮像環境を用いて画像を収集します。
「良品」画像だけでなく、検出対象となる「様々な種類の不良品」画像を、できるだけ多様なパターン(欠陥のサイズ、位置、形状、濃淡のバリエーション)で、バランス良く、大量に収集します。特に、発生頻度の低い欠陥や、判定が難しい境界線上の欠陥画像も重要です。
そして、アノテーションを行います。 収集した画像一枚一枚に対して、専門知識を持つ担当者(品質管理担当者や熟練検査員)が、正確に「良品」「不良品(欠陥種別)」のラベルを付けます。
必要に応じて、欠陥の位置や領域を矩形や多角形で囲む作業も行います。アノテーションの精度がAIの精度に直結するため、一貫性のある基準で慎重に行う必要があります。
AIモデルの学習と精度検証
収集・アノテーションしたデータを用いて、AIモデルを構築し、その性能を評価します。教師データをAIアルゴリズム(主にCNNなど)に入力し、ガラスの良品・不良品(および欠陥の種類)を識別するための学習(トレーニング)を行います。
そして、学習に使用していない「検証用データセット」を用いて、構築したAIモデルの性能を評価します。単なる正解率だけでなく、不良品の見逃し率(False Negative Rate / FNR)や、良品を誤って不良と判定する率(False Positive Rate / FPR)といった生産現場の実態に即した指標で評価することが重要です。
検証結果が目標精度に満たない場合は、以下を行い精度向上を目指します。
- 学習パラメータの調整
- 学習データの追加(特に誤判定した画像や、不足しているパターンの画像)
- アノテーションの見直し
- AIモデルの構造変更
このプロセスを繰り返し行います。
生産ラインへの実装と実運用評価
検証で十分な精度が確認されたAIモデルを、実際の生産ラインに導入します。構築したAI検査システムを生産ラインに物理的に設置し、PLC(Programmable Logic Controller)や搬送装置、既存の生産管理システム(MESなど)と連携させます。
不良品を自動的に排除する機構なども連動させます。
いきなり全自動化するのではなく、一定期間、既存の検査方法と並行稼働させたり、AIの判定結果を熟練者がダブルチェックしたりしながら、実環境での性能(精度、速度、安定性)を評価します。
本稼働後も、AIの判定結果やシステムの稼働状況を継続的に監視し、予期せぬ問題が発生しないか、精度が維持されているかを確認します。
運用体制の構築と継続的な改善
AIシステムを安定して運用し、長期的に活用するための体制を整えます。
システムの日常的な操作、簡単なトラブルシューティング(例: カメラレンズの清掃)、異常発生時の一次対応などを担当する現場オペレーター向けのトレーニングを実施します。
また、AIモデルのメンテナンスや再学習、専門的なトラブルシューティングを担当するエンジニアや品質管理部門との連携体制を明確にします。
製品仕様の変更や新たな欠陥の発生に対応できるよう、継続的にAIモデルを再学習・改善していくプロセス(MLOpsの考え方)を確立することが理想的です。
ガラス外観検査についてよくある質問まとめ
- ガラス外観検査においてAIを導入する主なメリットは何ですか?
従来の目視検査に比べ、AIは高精度で微細なキズや気泡、変色などを自動判別でき、検査漏れや過剰判定の低減、生産ラインでのリアルタイムな不良検出を実現します。また、作業者の負担軽減や生産効率の向上にもつながります。
- 既存の検査ラインにAIシステムを統合する際の主な課題は何ですか?
現行システムとの互換性、ガラス特有の光学的性質に対応する撮影環境の整備、そしてAIモデルの継続的なアップデート(再学習)が主な課題です。また、現場の作業員への操作研修やサポート体制の構築もスムーズな導入のためには欠かせません。
最も重要な準備の一つは、高品質な「教師データ」の収集と「アノテーション(教師付け)」です。検出したい欠陥を網羅し、良品・不良品のラベルが正確に付与された多様な画像データを大量に準備することが、AIモデルの精度を決定づける鍵となります。
まとめ
ガラス外観検査では、依然として目視検査が主流となっており、熟練技術者による柔軟な判断が可能な反面、照明条件やオペレーターの疲労に伴う検出漏れや不良品混入のリスクが常に存在しています。
このような問題に対応すべく、近年AIを活用した外観検査システムの導入が進められつつあります。AIは、大量の画像データを学習することで、微細な傷やヒビ、気泡といったガラス特有の複雑な欠陥を迅速かつ正確に検出します。
ご紹介した導入ステップは実践的な指針となりますが、扱うガラスの種類、求められる検査精度、既存ラインとの連携など、個別の状況に応じた最適なシステム構築やAIモデルのチューニングには、専門的な知識と経験が不可欠となる場合も少なくありません。
より具体的な導入計画や、自社の状況に合わせたカスタマイズ、技術的な課題についてさらに深く検討したい場合は、AI外観検査の専門家にご相談いただくことをお勧めします。
AI Marketで
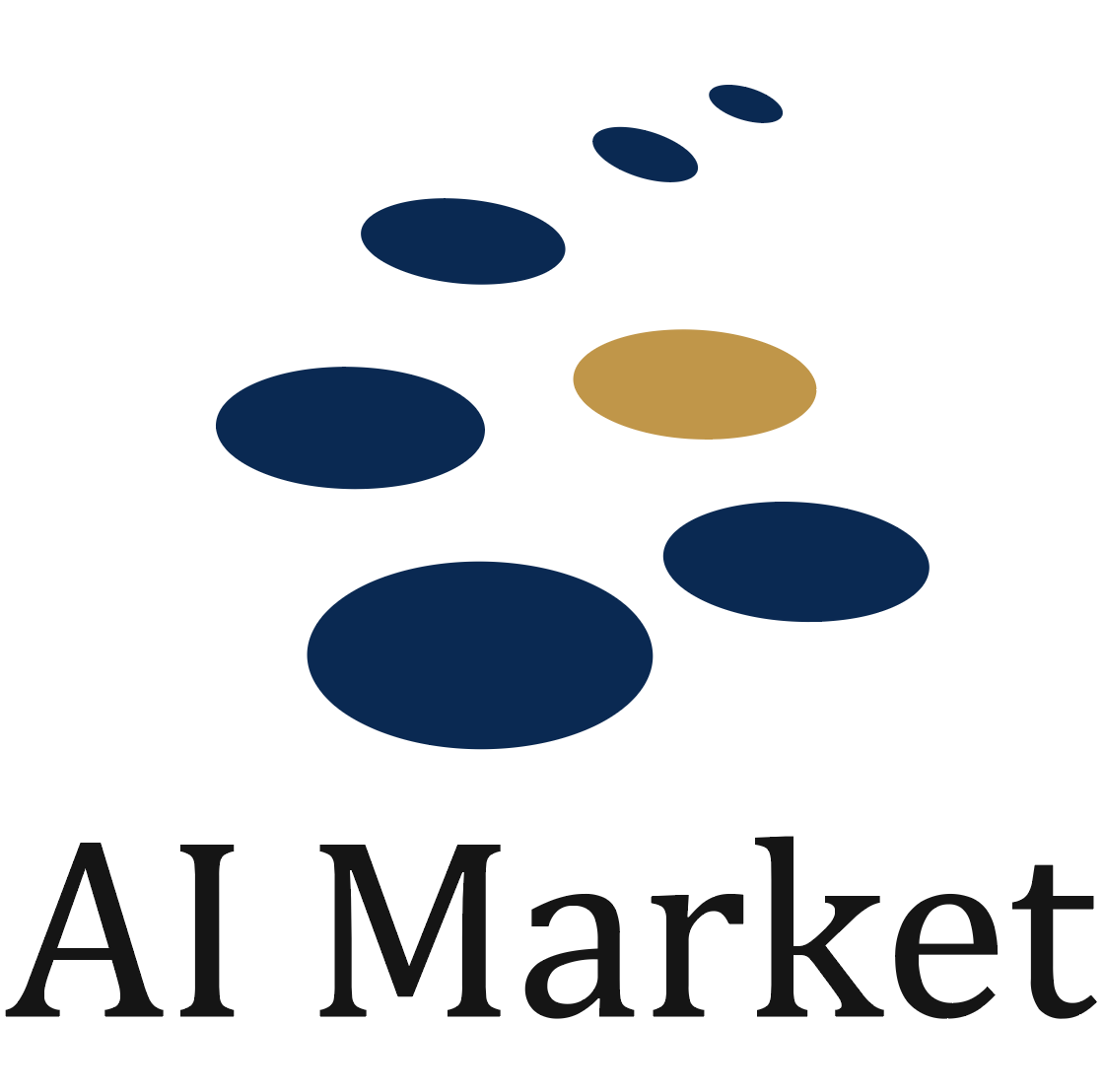
AI Marketの編集部です。AI Market編集部は、AI Marketへ寄せられた累計1,000件を超えるAI導入相談実績を活かし、AI(人工知能)、生成AIに関する技術や、製品・サービス、業界事例などの紹介記事を提供しています。AI開発、生成AI導入における会社選定にお困りの方は、ぜひご相談ください。ご相談はこちら
𝕏:@AIMarket_jp
Youtube:@aimarket_channel
TikTok:@aimarket_jp
運営会社:BizTech株式会社
弊社代表 森下𝕏:@ymorishita
掲載記事に関するご意見・ご相談はこちら:ai-market-contents@biz-t.jp
